Advanced avionics is no longer the domain of either military or commercial aviation; both civil and defense aircraft benefit from the latest technologies.
A growing number of aerospace technology companies are introducing avionics technology innovations for the benefit of civil and defense projects. In many cases, industry firms are facilitating fast and seamless technology transfer between aviation sectors, and modifying commercial off-the-shelf (COTS) avionics for military applications and vice versa.
"When it comes to commercial and military avionics technologies, there is huge potential for overlap," explains Steven Lien, vice president of marketing and product management for navigation subsystems and sensors at Honeywell Aerospace in Phoenix. "Obviously, some things need to be different, but there is a lot of commonality and many areas where both spaces, commercial and military, are moving forward together. We think about not 'either or' but really 'both together'-focusing on similar, sometimes common product roadmaps and common technology solutions that will serve both spaces, deliver the best of both worlds, and help customers be more efficient, safer, and accomplish their objectives."
Technology transfer
Many avionics technologies started in the military, were adopted and advanced in the commercial market, and moved back to the military. "GPS [global positioning system] technology started out with a military mission and was developed through the '60s, '70s, and '80s with that in mind, and migrated then to the commercial side," Lien says.
"Now it's ubiquitous and used everywhere from cars to cell phones to commercial aircraft, Lien continues." There are certain things the military has continued to evolve with GPS, and many others that commercial has continued to evolve, like augmentation, Wide Area Augmentation System (WAAS), and Localizer Performance with Vertical Guidance (WAAS LPV), and now rolling out Local Area Augmentation Systems (LAAS) with our SmartPath Ground Based Augmentation Sys- tem (GBAS) product.
"It's interesting," Lien adds. "GPS innovations that commercial [vendors] have driven over the past decade are moving back into the military. In fact, many commercial aviation technologies are being taken back into the military. We are seeing more and more of that, including military [customers] asking for civil certifications on their navigation boxes so they can fly in civil airspace.
"A number of militaries internationally and in the U.S. are thinking about interoperability," Lien notes. "They are asking for DO-178B and DO-254 [certification], which will make their navigation boxes interoperable in commercial airspace; ultimately, they want to be certified to automatic dependent surveillance-broadcast (ADS-B) Out mandates."
Later in this decade, the commercial market will start to roll out more constellations. "International militaries will pick that up because they'll want to use their home constellation. Militaries broadly will move beyond GPS to multi-constellation satellite navigation," Lien says. "It's interesting when you think about this juxtaposition between military to commercial development and then back to military, and how the two exist in many cases in parallel and in many other cases as one depending on the specific need and use case."
Flash FPGAs
A wealth of military applications use field-programmable gate arrays (FPGAs); at the same time, avionics engineers working on commercial aircraft are increasingly adopting FPGA technologies.
Flash-based FPGAs are being employed in a variety of commercial aviation applications, including new passenger aircraft and retrofit projects. Ken O'Neill, space and aviation director of marketing at Microsemi Corp. in San Jose, Calif., sees design activity today on new, modern commercial airliners and retrofit equipment for recently introduced airliners.
"In the case of retrofit design and brand-new design," O'Neill says, "we see Flash FPGAs being adopted and some older antifuse FPGAs being used. Our new family of 65-nanometer, Flash-based FPGAs are also starting to get some good design traction in new aircraft." The company's FPGAs are involved in the design activity around the Airbus A350, Airbus A400, and Boeing 787, as well as retrofit design activity on Boeing 737, Boeing 777, and Airbus A340 aircraft, he says.
FPGAs are being adopted in a lot of flight-critical applications, categories of equipment considered either Design Assurance Level (DAL) A or B, such as the primary flight computer, navigation system, cockpit displays, braking systems, cabin pressure and temperature, lighting, actuator controls, or aircraft engine controls. "In those kinds of applications, very often there's a requirement for redundancy, so there will be at least two instances of the equipment on the aircraft," O'Neill explains. "There's often a requirement for those two pieces of equipment to have been designed independently by different design teams and to use different components, so that there's no common failure mode between the two types of equipment."
Engineers selecting FPGAs in these applications often will choose one particular kind of FPGA for the primary and a different type of FPGA for the redundant version of the system, O'Neill says. "That requirement for dissimilarity is one of the things driving adoption of new and not-so-new FPGAs. The fact that our Flash FPGAs and antifuse FPGAs are manufactured differently and have different architectures and different software means they are entirely dissimilar and, therefore, can participate in both sides of this redundant equipment."
Providing protection
Safety is a serious concern in civil and defense aviation applications; as a result, safety-related attributes can factor heavily in the adoption of certain avionics. Of particular interest are those avionics technologies that deliver protection from atmospheric radiation, lightning, and the like.
"Even at 30 or 40 thousand feet in the atmosphere, where commercial aircraft fly, there are significant quantities of neutrons in the air and they're energetic. They can strike data circuits and cause data to change, upsets to occur," O'Neill explains. FPGAs configured with SRAM cells are susceptible to upsets; SRAM cells will upset in neutron radiation, causing the FPGA to change state and become nonfunctional, he says. "That is a major concern if you're using the FPGA for an application which is flight critical, and people's lives depend on the FPGA working correctly. The Flash-based FPGAs and antifuse FPGAs that we offer are immune to configuration upsets due to the neutron radiation that you get in atmospheric applications."
Engineers have employed Micro- semi FPGA technology in various military fighter, bomber, transport, tanker, and support aircraft and myriad programs, including modern U.S. fighter programs like the F-35 and F-22, upgrades on the F-16 and F-18; internationally, the Eurofighter Typhoon has a significant number of Microsemi FPGAs on board, O'Neill says.
Microsemi's patented plastic large area device (PLAD) package technology, used in the company's transient voltage suppressor (TVS) diodes, help protect aircraft from multi-stroke lightning. "TVS diodes protect various electronic systems-such as those used in power management, actuation, flight control, and engine management-from transient voltage surges," says Durga Peddireddy, director of marketing and applications at the Microsemi Hi-Rel Group in Lawrence, Mass.
"The single-component solution meets aircraft lightning standard RTCA DO-160, saves board space, lowers weight, and improves reliability over the multi-device designs often used to provide these high levels of protection," Peddireddy adds. "It has dual usage because any aircraft, either military or commercial, need protection from lightning strikes." It brings value to all aircraft modules and subsystems from manufacturers such as BAE Systems, UTC, and Rolls Royce, Peddireddy adds.
Upgrades and integration
Commercial and military pilots are anxious to gain access to the latest cockpit avionics; yet, the current economic environment is oftentimes preventing the acquisition of new aircraft and glass cockpit upgrades on commercial and military aircraft.
"The military space is really interesting right now," says Larisa Parks, vice president of marketing and product management for crew interface products at Honeywell Aerospace. "Certainly, the current economic and budget situation for the defense sector in the U.S. is limiting the new cockpit opportunities, but there is a desire and need to upgrade, for a couple reasons: to incorporate some of the NextGen [Next Generation Air Transportation System] functionality as they plan to mix airspace, and also reliability and performance. They're looking for those types of upgrades in the pilot experience without swapping out the entire cockpit." Avionics engineers are implementing solutions such as Honeywell's IPM (image processing module) to improve the processing power in existing cockpits.
Mandate-driven modifications
Some avionics upgrades are driven by mandates, such as NextGen in the U.S. "It's usually collections of mandates that tip the scales as to when it is time to replace an analog cockpit or legacy CRT display, and how far modifications go or the point at which it's no longer economic to retain a legacy system," says Paul Hart, director of avionics engineering at Curtiss-Wright Controls Avionics & Electronics (CWC-AE) in Christchurch, England.
US Airways reportedly is the first commercial airline to receive FAA certification on the full suite of SafeRoute NextGen ADS-B avionics, in which military avionics engineers are becoming increasingly interested. US Airways engineers selected SafeRoute, a set of four flight deck applications from ACSS, an L-3 Communications and Thales Company in Phoenix, for its wide-body Airbus A330 aircraft to enhance operational safety and efficiency in all phases of flight under the FAA's NextGen implementation program.
"The recent certification of ACSS NextGen avionics for US Airways is an important advancement in cockpit avionics," notes Steve Henden, senior manager, communications for L-3 Aviation Products in Phoenix. "The higher level of situational awareness and information enables our SafeRoute ADS-B In avionics to deliver efficiency and safety benefits, resulting in less fuel burn and fewer deviations during approach."
The certified SafeRoute suite of applications on US Airways A330 aircraft uses Automatic Dependent Surveillance-Broadcast (ADS-B) technology to provide pilots with more precise position information of the operating aircraft and surrounding airplane traffic. ADS-B is a cornerstone technology for the FAA's NextGen airspace redesign program.
"US Airways and our other airline partners understand and embrace the opportunities and savings ADS-B provides for operators," says Terry Flaishans, president of ACSS. "Our investment in SafeRoute avionics is helping airlines operate more safely and fly the most efficient routes to their destinations."
Modular avionics
Modification centers and original equipment manufacturers (OEMs) are installing glass cockpits under a growing number of aircraft upgrade programs, says CWC-AE's Hart. Yet, the industry trend toward glass cockpits creates a lot of design and integration issues.
"The interfacing on a lot of the avionics, such as the electronics flight instrument system (EFIS), is ARINC 429, Ethernet, or sometimes video buses. They don't normally have the analog connections needed to interface to legacy aircraft, and that's really where we come in," Hart explains. "A lot of EFIS have a generic multifunction display but the digital receiver ports won't be compatible with a lot of sensors-for position, airspeed, altitude, pressure, etc.-around the aircraft. It would be a very expensive retrofit to replace and recertify all those sensors; we provide the translation box that cleans up those interfaces, does all the signal conditioning and scaling, and sends a clean output by ARINC 429 or Ethernet into the glass cockpit EFIS."
Avionics upgrades often happen in stages. "There are a lot of existing systems on the aircraft-many of which will not necessarily be upgraded at the same time-that they will want to reuse from program to program," says John Fallon, marketing manager at Curtiss-Wright Controls Avionics & Electronics in Dublin. "The data concentrator can be the glue and remove the complexity for the core avionics supplier. They can continue to develop new systems and hand off the custom integration with other systems to data concentrators. A data concentrator solves this integration challenge by collecting, combining, and reformatting data from a variety of existing subsystems into the required avionics bus format."
"What we have is a scalable DCU approach; people can do a basic cockpit upgrade, gaining navigation and primary flight display information, and still retain a mix-hybrid cockpits that maintain a mixture of glass cockpit and old analog displays," Hart says. "With a DCU architecture, you add capability to a bus so you can then go into higher levels of integration and start phasing out some of the old analog systems. There are ways and means that cockpit upgrades can be phased in conjunction to mandates and aircraft owners' budgets."
"Our Data Concentrator Unit (DCU), has been described by some in the industry as a 'Happy Box' because it solves many integration issues and lowers certification risk to the program," Fallon says. "A DCU converts input data from one form to another before outputting to one or more locations. Honeywell engineers chose Curtiss-Wright's Advanced Data Acquisition Units (ADAUs) to convert analog and digital sensor inputs into digital outputs on its Primus Apex Integrated Flight Deck.
"It's about taking an existing product, the standard data acquisition unit; making it more powerful; and enabling growth features that increase efficiency, capacity, and most importantly, enhance aviation safety. There's a solid trend throughout the industry toward making integrated avionics systems more aircraft-independent and Honeywell's ADAU concept makes this a reality," says John Todd, vice president of business and general aviation at Honeywell Aerospace.
"The ADAU approach plays a critical role in enabling Primus Apex to reduce the time and costs associated with adopting and certifying highly integrated, custom avionics suites," Todd continues. "By having the aircraft-specific data conversion done separately from the flight deck, OEMs and operators benefit from an easier and more straightforward path toward incorporating highly-desirable features such as low RNP (required navigation performance), ADS-B, or SmartView enabled by software upgrades."
Military aircraft already are benefiting from existing data concentrator technology to solve integration challenges as part of major upgrade programs, Fallon says. Curtiss-Wright has provided data concentrators to the CH-47 and CH-53 military helicopter upgrade programs.
"The latest generation of the data concentrator is also being provided to the U.S. Air Force and NATO Airborne Warning and Control System (AWACS) upgrade programs," Fallon says. "Rockwell Collins is providing the navigation and control avionics upgrade and is using CWC-AE DCU technology." Curtiss-Wright's DCUs provide the conversion of analog and digital sensor inputs into digital outputs to support the upgrade of the AWACS aircraft's vital navigation control avionics.
Design to delivery
To help avionics systems developers fast-track the design-to-deployment process of flight communication and wireless server applications, Kontron in Poway, Calif., launched the next generation of its ACE Flight 600 general-purpose airborne servers.
The Kontron ACE Flight 600 integrated, application-ready platform is designed to meet advanced communication application requirements for Ethernet-based network installations on linefit and retrofit aircraft.
"Although the primary applications for Kontron's ACE Flight Server and Cab-n-Connect wireless access point equipment have been for commercial airlines and general aviation, some deployments are in progress for government and military aircraft," says R.J. McLaren, product marketing manager at Kontron. "A general-purpose networking server can be used for many applications and provides up to 1.8 terabytes of solid-state disk (SSD) storage. In combination with the wireless access point, it allows for an enterprise-class wireless networking solution on a plane that has been tested and approved by the FAA (PMA)."
A majority of engineers use this combination of Kontron avionics equipment for passenger in-flight entertainment or Internet connectivity; yet, it is also used for crew connectivity and aircraft operations.
"Militaries and governments continue to use personnel electronic devices that need to be continuously connected. Our products can help to provide secure wireless on the plane and ensure that they continue to get high data rates for video or other types of media streamed to their portable wireless devices," McLaren adds.
"The challenges for both civil and military continue to be savings in weight, power, size, cost, and time-to-market with new technologies. The process and cost required to get new equipment approved and certified for airworthiness, not to mention the down time to install onto an aircraft, makes it difficult to keep ever changing and evolving technology for the consumer current on the aircraft," McLaren says.
"To help solve some of these issues, Kontron develops computer on modules and boards that can be used for avionics and provide compatibility both backward and forward within the deployed equipment," McLaren notes. "By packaging cutting-edge processor boards in pre-certified solutions, Kontron makes it even easier for the avionics industry to adapt and deploy new technology onto the plane, saving significant time and costs by doing it themselves."
Future functionality
Avionics technology continues to advance rapidly, to the benefit of commercial, general, and military aviation communities and applications.
"I see a bright future in spite of various challenges such as reducing weight, higher reliability, increasing efficiency, high power requirements, and lowering costs the civil and military avionics is facing," says Microsemi's Peddireddy.
"New architectures, such as distributed control systems, all-electric systems, modular approaches, lighter body materials, and next-generation semiconductor technologies, are a few approaches to address these challenges," Peddireddy explains. "Engineers play a vital role in meeting these demands by being more innovative and agile."
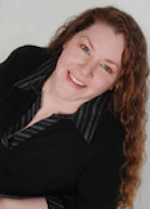
Courtney Howard | Executive Editor
Courtney, as executive editor, enjoys writing about all things electronics and avionics in PennWell’s burgeoning Aerospace and Defense Group, which encompasses Military & Aerospace Electronics, Avionics Intelligence, the Avionics Europe conference, and much more. She’s also a self-proclaimed social-media maven, mil-aero nerd, and avid avionics geek. Connect with Courtney at [email protected], @coho on Twitter, and on LinkedIn.