NASHUA, N.H. - The embedded computing chassis, enclosures, and backplane databus industry is on the verge of a technology revolution every bit as significant as the industry’s transition to VPX nearly two decades ago, as standard architectures and small-form-factor designs are poised to become major players in this market.
First, open-systems standards based on the Sensor Open Systems Architecture (SOSA) are inundating embedded computing bus and board designs like a tidal wave, as new SOSA-aligned products enter the market virtually every week. Second, the SOSA-compliant VNX small-form-factor bus and board standard is making significant improvements in power, performance, and thermal management to take a commanding market role beginning as early as this year.
As SOSA-aligned enclosures, chassis, and backplane databuses become widely available, not only will the industry see an increase in compatible productsIn addition to SOSA-aligned and small-form-factor chassis, enclosures, and backplane databuses, industry trends also include the addition of RF and microwave coax interfaces for boards and enclosures, a new crop of no-slot interfacing, innovative thermal-management design approaches, and improved interconnects for advanced signal integrity for applications such as artificial intelligence (AI) and machine learning, fast Ethernet interconnects, and small-form-factor avionics, vetronics, small satellites, and unmanned vehicles.
SOSA and open-systems standards
Not only does SOSA have a big influence on chassis and backplane databus design today, but the Modular Open Systems Approach (MOSA), The C5ISR/EW Modular Open Suite of Standards (CMOSS), Future Airborne Capability Environment (FACE), the Hardware Open Systems Technologies (HOST), and similar established or emerging electronics-design standards also are taking-on important roles.
“Today it’s all about SOSA, MOSA, and FACE,” says Lino Massafra, vice president of sales and marketing at embedded computing specialist North Atlantic Industries in Bohemia, N.Y. “From a software standpoint it’s FACE. We will align to the SOSA profiles and high-density I/O profiles. We are introducing new chassis with the SOSA profiles in mind.”
SOSA is evolving into the dominant standard, with other military service-specific established and emerging standards flowing toward the SOSA banner. “There is customer demand for SOSA,” Massafra says.
It’s all based on SOSA. The Army, Navy, and Air Force have their pieces of it, and they are bringing it under SOSA.”
It’s becoming difficult even to avoid the mention of SOSA in embedded computing discussions. “SOSA is still the story of the day,” says Mark Littlefield, senior manager of embedded computing product and system solutions at chassis and enclosure specialist Elma Electronic in Fremont, Calif. “Every day I get asked questions about SOSA and how to use SOSA. There continues to be growth and interest in that, and SOSA 1.0 made people believe SOSA is on a growth path. There is a lot of product out there and more every day.”
Last September The Open Group in San Francisco — the standards organization that oversees SOSA — published the first official version of the SOSA technical standard to help reduce development and integration costs for military capabilities and to reduce time to field.
SOSA 1.0 seeks to streamline U.S. military capabilities by enabling rapid, affordable, cross-platform capabilities based on best practices of system, software,The new standard encapsulates fundamentals of Modular Open Systems Approach (MOSA) design to develop embedded computing solutions for military applications that involve a unified set of sensor capabilities.
The SOSA Consortium aims to create a common framework for moving electronics and sensor systems to an open-systems architecture based on key interfaces and open standards established by industry and government consensus.
The open architecture supports aerospace and defense applications for manned and unmanned surface vessels, submarines, aircraft, land vehicles, and spacecraft. The goal is to reduce development and integration costs and reduce time to field new sensor capabilities.
With the new SOSA 1.0 standard in place, The Open Group is formalizing compliance testing to enable embedded computing manufacturers to meet guidelines of the SOSA standard. Those introducing products intended to meet the standard but that have not gone through compliance testing will be considered SOSA-aligned.
One large trend in the embedded computing chassis and backplane industry “certainly is the evolution of SOSA,” says Justin Moll, vice president of sales and marketing at chassis and enclosure specialist Pixus Technologies Inc. in Waterloo, Ontario.
“All these companies out there that typically have some sort of proprietary solution for RF and signal process are all trying to develop SOSA-based solutions, and that will continue as these are evolving into MOSA,” Moll says. That certainly is a trend.”
MOSA is a technical and business strategy — not an actual industry standard — for designing an affordable and adaptable system, and is the Pentagon’s preferred way to design open systems solutions. MOSA encourages a modular design that uses major system interfaces between a system platform and a major system component, between major system components, or between major system platforms.
MOSA uses a system architecture that enables systems designers incrementally to add, remove, or replace major system components throughout the life cycle.
MOSA enabling standards are widely accepted, supported, and consensus based standards, such as SOSA, that support interoperability, portability, and scalability. Falling within the MOSA umbrella are standards such as SOSA, CMOSS, FACE, and Vehicle Integration for C4ISR/EW Interoperability (VICTORY).
The move to MOSA-like open-systems standards is likely to continue indefinitely, “and we will ride this SOSA wave for a while,” Pixus’s Moll says. “Certainly the higher speeds for the backplane, like 100 Gigabit Ethernet, optical, and RF will provide very high performance. We will be riding that wave for a bit.”
More standardization
MOSA and its companion standards are not the only areas where military embedded computing designers are looking to capitalize on standards. The U.S. Army Program Executive Office for Ground Combat Systems (PEO-GCS) in Warren, Mich., oversees a standard for the size of vetronics components called the Standard A-Kit Vehicle Envelope (SAVE), which concerns mounting size and power needs, explains Jason DeChiaro, system architect for the Curtiss-Wright Corp. Defense Solutions division in Ashburn, Va.
SAVE is targeting new platforms, and existing platforms as they are upgraded, DeChiaro says. “This reflects to momentum to MOSA,” he continues. By defining a space claim in connectivity, you are defining a space for these components. It defines a maximum envelope for systems, and what you can put in the box.”
SAVE does not specify other standards such as CMOSS or SOSA; it simply defines standard spaces for electronics boxes. “It can be limiting in some ways, because we can’t do these larger solutions, but it does give us a known size target to hit,” says Dominic Perez, chief technical officer at Curtiss-Wright. “It provides a known footprint for upgrades.”
In addition, SAVE “makes it easier for us to be CMOSS and SOSA compliant, which is the goal of MOSA,” DeChiaro says. It’s the need to cram as many electronic systems in to military land vehicles today that is driving Army experts toward standards and guidelines like SAVE, CMOSS, and SOSA. “The ground vehicle is the command post of today and the future,” Perez says. “We are pushing a lot of electronics into those vehicles, which also pushes for communications networks.”
Small form factors
Following closely in importance behind the move to open-systems standards are trends in small-form-factor chassis, enclosures, backplane databuses, and circuit boards. At center stage of this assault on size, weight, and power consumption (SWaP) is the so-called VITA 74 VNX form factor, which calls for circuit boards about the size of a deck of playing cards — or roughly one-third the size of 3U VPX cards and enclosures. VITA is the Open Standards, Open Markets trade association in Oklahoma City.
“Small form factors like VNX have started up again in earnest,” says Elma’s Littlefield. “VNX is a little less than one-third the size and volume of 3U VPX, and you will see first products before the end of the year. It’s still not taken off yet, but enough people are interested in the standard that there will be traction.”
While VNX went up on the drawing board a decade ago as a smaller, less powerful, and more power-efficient version of VPX, industry experts say early indications are that VNX soon not only will be able to accommodate some of the most powerful embedded computing processors, but also handle advanced cooling and thermal management designs to enable this form factor to handle upwards of 100 Watts per card.
“VNX was originally envisioned as a way to make small mission computers,” Littlefield explains. “That is still very much the model. Also, designers are finding there are some applications that require a substantial amount of processing that 3U VPX just doesn’t fit.”
Among those potential applications for VNX are three-inch tubes that house tactical missiles; small unmanned vehicles for land, sea, and air; high-performance sensor pods for fixed-wing aircraft, helicopters, and unmanned aerial vehicles (UAVs); and handheld flight-line test and measurement instruments that could replace two-person-carry and rolling systems.
Among the original developers of the VNX form factor is Bill Ripley, director of embedded computing consultant Brame Technologies in Albuquerque, N.M. Ripley says VNX has been picked up by SOSA. To get SOSA acceptance “we took VNX and redefined it to use the same tenets as VPX to go relay out to its connector interface. While we were there, we decided to revise VNX to be SOSA compliant by re-evaluating the pin assignments we had for the best-possible signal integrity to guarantee higher bus speeds.”
In addition, Ripley and his colleagues at VITA were able to redefine the VNX interconnect interface to accommodate a family of connectors to bring RF coaxial cable and optical interconnects into the VNX specification. VNX cards are smaller than 3U VPX, but use the same bus structure.
VNX was designed originally about eight years ago to accommodate the mid-level Intel Atom processor, yet industry designers are working on versions today that eventually will be able to handle high-end processors approaching the performance of the Intel Xeon.
If that happens, then the next question is will VNX be able to accommodate the thermal management and electronics cooling necessary for the most powerful processors? Ripley says it will. “We’re looking at significantly higher power than we had in the original standard,” he says. “The VNX module was built from the ground-up to be conduction cooled, but we don’t use wedge locks in the system. We can move heat out to heat sinks along the card’s left face, right face, and handle face. All paths can carry heat away from a system using fins, cold plate, liquid cooling, or forced air.”
So with all this going for it, will VNX be able to replace 3U VPX altogether. Ripley says the answer is no. “There is so much momentum going on with VPX, and VNX is not intended to replace VPX, but is intended to bring VPX-like capabilities down to the small-form-factor market.
One advantage of designing VNX and 3U VPX to be so closely related is the ability to use VNX and 3U VPX boards together in one hybrid enclosure. “Over time they could shrink the box down to a VNX size,” Ripley says. “The connectivity is close enough to 3U VPX to be able to change it from VPX to VNX.”The Elma VITA 48.8 Air Flow-Through development platform, is for developing and testing boards used in air-flow-through systems.
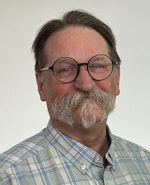
John Keller | Editor-in-Chief
John Keller is the Editor-in-Chief, Military & Aerospace Electronics Magazine--provides extensive coverage and analysis of enabling electronics and optoelectronic technologies in military, space and commercial aviation applications. John has been a member of the Military & Aerospace Electronics staff since 1989 and chief editor since 1995.