For years, a consortium of experts in the defense technology business have worked to roll out an open-systems industry standard dubbed the Sensor Open System Architecture (SOSA). The high-level goals of SOSA include openness and being platform- and vendor-agnostic while being aligned with Modular Open Systems Approach (MOSA) using standardized software and hardware. The consortium aims to leverage existing and emerging open standards and align with DOD service objectives. Finally, SOSA aims to keep technology affordable and adaptable.
The consortium, called the Open Group in San Francisco, unveiled its SOSA 1.0 standard in the fall of 2021, and that open architecture remains a major driving force in industry trends in the development of deployable rugged computing systems.
Justin Moll, vice president of sales and marketing at Pixus Technologies Inc. in Waterloo, Ontario, notes that the SOSA efforts have been front of mind as engineers build components for defense system.
"A key question in defense-based embedded computing systems is whether it is required to be SOSA-aligned or not," Moll explains. "If SOSA aligned, there is constant drive for performance within the typical space limits of deployed systems. For chassis platforms, this greatly affects how we balance the thermal management, I/O configuration including fiber and optical interfaces, backplane speeds, chassis management, etc. If the project is not SOSA aligned, there is a broader spectrum of performance criteria from lower end to very powerful systems without the potential restraints of falling within a specific profile."
The Open Group says that systems designed with SOSA in mind finally will be able to put their technology to the test -- literally -- to see if it meets muster to be called conformant to the standard. While SOSA is working to create its Conformance Test Tool Framework to automate the process, when testing initially rolls out -- possibly as early as February 2023 -- it will be more of a manual process.
With SOSA in mind, Pixus introduced its SHM300 SlotSaver VPX VITA 46.11-compliant chassis manager that enables embedded computing designers to manage the chassis without sacrificing a slot.
The SHM300 is designed to the latest SOSA requirements, and uses all U.S.-based software and firmware. The chassis manager monitors and manages the field-replacement units plugged into the SOSA/OpenVPX chassis.
Features include chassis discovery of plug-in boards, information storage, cooling management, SDR-based sensor initialization, and other chassis control and event handling.
The compact design of the Pixus SOSA-aligned chassis manager ensures that the size and spacing do not interfere with VITA 66 or 67 interfaces and cabling. The SHM300 also supports redundant options.
Bringing the heat
Pixus's Moll says that SOSA conformance is adding a bit of a wrinkle to a problem that has kept engineers up at night: how do we keep this technology cool enough?
Aneesh Kothari, vice president of marketing for Systel Inc. in Sugar Land, Texas, agrees that thermal management remains a massive consideration in the mil-rugged development world.
"A senior leader from the U.S. Army stated, 'On the combat side, the biggest challenge we face is cooling. We operate under armor and most of our systems are reduced in size and cannot provide the airflow you find in the commercial sector.' At Systel, we have found that to be absolutely true in our approach to system design and testing; the most significant consideration for forward-deployed hardware is accommodating for the heat demands of powerful electronics," Kothari says.
"We integrate high-wattage commercial electronics into our edge server-class systems, with a single GPU producing up to 300 Watts and some total system wattages approaching 1000 Watts," Kothari continues. "Reliably dissipating that amount of heat in a sealed system which is exposed to high operating temperatures -- routinely 55 degrees Celsius and up to 75C in extreme applications -- is paramount. In our designs, we carefully consider wattage and junction temperatures of every component on every board in the system. We design for absolutely worst-case conditions, making no assumptions on customer-provided cold plates or available air flow. Our thermal management is self-contained to the computer; it’s the best way to ensure reliability."
Kothari concludes, "On average, the next generation of CPUs, GPUs, NICs, FPGAs, and other electronics will produce more heat than the current generation; this will continue to pose a significant challenge. Thermal management is a critical decision variable and a major source of program risk if not properly engineered and tested for."
Piece of Pi
Last year marked the tenth anniversary of Raspberry Pi small-form-factor single-board computer. The "RPi" was launched with computer science education inLast year, Curtiss-Wright Defense Solutions in Ashburn, Va., brought the Raspberry Pi to the world of rugged computing for aerospace and military applications.
David Jedynak, general manager of the Parvus business unit of the Curtiss-Wright Corp. Defense Solutions segment, explains that the company's DuraCOR Pi Raspberry Pi Mission Computer addresses a need for a rugged, ultra-small form factor, lower-cost computer board that isn't overpowered for the task it is asked to do.
"Full military, rugged standards -- the whole works," says Curtiss-Wright's Jedynak. The DuraCOR Pi has undergone qualification testing per MIL-STD-810, MIL-STD-461, MIL-STD-1275, MIL-STD-704, and RTCA/DO-160 conditions for environmental, power, and EMI compliance.
The Raspberry Pi-enabled rugged mission computer is small enough to fit in the palm of a hand; it weighs half a pound, and measures 1.2 by 2.49 by 3.34 inches. It can be stacked to extend functionality and performance via an expandable ring system design that enables system designers to configure the mix of DuraCOR Pi mission computers and hardware attached on top modules.
The DuraCOR Pi also can combine in a stack with the miniaturized Parvus DuraNET 20-11 network switch, which provides carrier-grade Ethernet software Level-2+ management and support for IEEE-1588v2 precision timing protocol.
DuraCOR Pi is able to run Pi operating systems such as NSA STIGd Raspian Linux, VxWorks, Windows and IoT Core, as well as Pi toolsets, and programming frameworks like Python, Java, C, and C++.
"Security is obviously really important," Jedynak says of the DuraCOR Pi. "One of the things that's available -- there are various organizations who provide lockdown versions of the Linux that's on the Raspberry Pi. One of our goals in all of this is to make sure that the standard Raspberry Pi ecosystem, all the software, all those sorts of things, it's 100 percent read across.
We're not going and trying to do something custom with all that, Jedynak continues. "In fact, the benefit is you can go grab a commercial Raspberry Pi. It's just an off-the-shelf one that you would use. You go and buy it online or in a big box store, go get that, you can do all your development, then you take ours, you can just move it right over without a bunch of changes. And that way you can leverage all the strength of the ecosystem that's already doing things to harden the Raspberry Pi's operating system and other software."
Printing parts
A benefit of SOSA is having vendor-agnostic components that can be replaced on-the-ground without having to be shipped stateside or off base. That same mindset is being embraced outside of SOSA when it comes to additive manufacturing -- also known as "3D Printing."
Panasonic Corp. of North America in Newark, N.J., sees its TOUGHBOOK 40 as a technology that will put the power of 3D printing into the hands of warfighters when time is of the essence when they are deployed away from a supply depot.
Valerie Flores, executive account manager for Navy/USMC federal mobility at Panasonic Connect, says that their customers seek to leverage technologies like artificial intelligence (AI), augmented reality (AR), and additive manufacturing.
"And that requires a high-performance device capable of handling graphic, intense applications," Flores says of AI, AR, and 3D printing. "So, take additiveFlores explains another trend in rugged computing solutions is the requirement for scalability and future-proofing.
"So, all of our customers, I think they have always been they're looking for ways to optimize their budget, so the decisions they make today will be capable of supporting their missions tomorrow," Flores says. "And one of the key features in the TOUGHBOOK 40, the design gives them eight modular areas, including modular expansion packs. And since these are user-upgradable, our customer can change out and customize these areas, such as optical drive, smart card readers, I/O ports, barcode readers, and even the keyboard. So, the modular design not only offers our customers extreme flexibility to meet changing requirements, but it also enables sustainment to improve efficiency. And as you know, a lot of our customers are in remote locations or they're on long deployments where this feature is critical because they can change it out and they get their users back up and running."
Rugged unmanned
Technology that is driving the revolution of unmanned military systems is enabled by the compute power delivered by rugged embedded computers that can operate in the harshest of environments.
"The proliferation of unmanned vehicles and autonomous capabilities is driving the need for higher performance electronics in ultra-compact form factors," says Systel's Kothari. "It’s the fundamental push to do more with less. Platforms are becoming more densely sensored and more connected across the battlefield. Especially when you talk about unmanned, you have vehicles that are smaller and can range further than manned vehicles. The computer hardware and electronics architectures that power these missions have to be SWaP-optimized and MIL-SPEC rugged with extended capabilities; in effect taking data center performance and putting it out to the edge. Successfully harness and exploiting sensor data at the edge must be done 'on-prem'; it can’t be sent to the cloud because of latency, bandwidth, and security considerations. Small and rugged-edge computers is the solution to the emerging problem set of conducting tactical AI edge processing for data-centric operations."
Systel's fully-rugged Kite Strike II small form factor embedded computing solution integrates the latest NVIDIA Jetson AGX Orin embedded AI compute module which features up to 275 TOPS of performance.
"Kite-Strike II is purpose-built to conduct tactical AI edge processing for data-centric operations in austere environments, and offers 10Gbe TSN-compliant capability, allowing data to be pushed through in-vehicle networks in a JADC2 environment," Kothari says. "In a battlespace where every soldier and vehicle is a sensor, actionable data and interconnectivity are critical. Kite-Strike II is a complete compute at the sensor solution, reducing overall equipment SWaP by integrating AI processing, high-bandwidth networking, high-speed and secure storage, robust IO, and modular expansion capabilities in a single line replaceable unit (LRU)."
Who's who in rugged computing
Abaco Systems
Huntsville, Ala.
Â
Aitech Defense Systems, Inc.
Chatsworth, Calif.
Â
Curtiss-Wright Defense Solutions
Ashburn, Va.
www.curtisswrightds.com
Â
Combat Proven Technologies (CP Tech)
San Diego
Â
Core Systems
Poway, Calif.
Â
Crystal Group Inc.
Hiawatha, Iowa
Elma Electronic
Fremont, Calif.
Â
Extreme Engineering Solutions (X-ES)
Verona, Wis.
Mercury Systems
Andover, Mass.
Â
PacStar
Portland, Ore.
Â
Panasonic Corporation of North America
Newark N.J.
Â
Pixus Technologies Inc.
Waterloo, Ontario
Â
Samsung Electronics America, Inc.
Ridgefield, N.J.
Â
Systel Inc.
Sugar Land, Texas
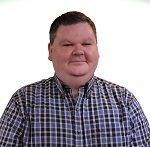
Jamie Whitney
Jamie Whitney joined the staff of Military & Aerospace Electronics and Intelligent Aerospace. He brings seven years of print newspaper experience to the aerospace and defense electronics industry.
Whitney oversees editorial content for the Intelligent Aerospace Website, as well as produce news and features for Military & Aerospace Electronics, attend industry events, produce Webcasts, oversee print production of Military & Aerospace Electronics, and expand the Intelligent Aerospace and Military & Aerospace Electronics franchises with new and innovative content.