The New Year is often a good time to try new things. It could be, for example, that you’ve evaluated OpenVPX in the past, but never taken it past the evaluation stage. Or it could be that its unfamiliarity meant that it appeared to be awkward to use. Perhaps you’ve used VME or CompactPCI in the past, but you now have a project in which minimal size, weight and power is a key requirement – and you have some great software that needs to be deployed on a rugged platform. Perhaps it’s time to revisit OpenVPX as an option?
This short guide is designed to help you get started – and explains how Abaco can make it even easier for you.
Step One
Identify what your processing requirements are. This may seem obvious, but there are several processor architectures you can choose from: Intel, PowerPC and ARM. Each will have different core counts and clock frequencies - but be aware that not all processors can run all operating systems. For Windows, you will be limited to Intel - but for Linux, pretty much anything goes. Is your application thread-aware and will it benefit from a higher core count? It’s not sufficient that the operating system is SMP (Symmetrical Multi Processing) capable; you will have to work to parallelize your application code using threads or OpenMP. Maybe look as utilizing SIMD (Single Instruction Multiple Data) type functionality on Intel AVX512 or AltiVec on PowerPC.
For determinism and real time performance, one of the popular real time operating systems can be tailored to meet your requirements and most will run on multiple architectures: think VxWorks, LynxOS, INTEGRITY and so on For avionics safety certification, take a look at the QorIQ PowerPC processors such as are featured on the SBC314 with its quick start time and certification artefacts. If you need maximum performance, the latest Intel processors give the best performance per watt. If you need more processing power, consider adding a GPU for accelerated graphics or parallel processing using CUDA: there is always limit to what the CPU can do...
Step Two
Address your I/O requirements and consider your thermal cooling solution. This will narrow down your options to a set of possible processor boards. As a general rule, the smaller 3U boards can dissipate around 75 watts and the larger 6U boards around 150 watts, depending on the type of thermal solution used (convection or conduction). 6U boards have more I/O and dissipate more power for maximum performance. Some of our newer conduction-cooled boards now include heat pipes (such as the SBC347D) which is a more efficient thermal solution, allowing the boards to run faster (and hotter).
For the I/O, check the configurations guides to see what I/O options are available on the board. If the board has all the I/O you need, you simply need to identify the correct rear transition module (RTM) to match the board and provide all the I/O on standard connectors. If you require special interfaces or more of a certain type of I/O, don’t panic - there are a large number of expansion boards available in PMC and XMC format to allow for I/O expansion (much like PCIe cards in a PC). If you don’t see something that will meet your needs, then speak to your local applications engineer for guidance. It may be possible to get a custom option or integrate a new board to meet your I/O requirements. Our applications engineers are a great source of knowledge and will provide detailed technical support, visiting you onsite if needed.
Step Three
Now’s the time to pull it all together. This can be the most onerous task, depending on the system complexity - but there are off-the-shelf solutions that will allow you to get up and running in the lab quickly. The OpenVPX specification extends to backplanes and chassis and common configurations can be purchased off-the-shelf. Backplane profiles allow for small and large cluster configurations to meet a variety of needs. From three to 21 slots, the OpenVPX specification has modularity built in, allowing boards from different vendors to be rapidly integrated and deployed.
The simplest system may just consist of a single PC-type Intel board with integrated graphics - much like a laptop computer with a single mezzanine site. The system below shows such a system with all the I/O integrated into the box (3U VPX SBC328). These systems are quick and easy to put together and can be done with a limited amount of hardware experience (just a few screws). Much like building a PC, it’s plug and play all the way.
If you have a requirement for a VPX board and want to evaluate solutions from Abaco Systems, either click on the “Contact An Expert” button on any of our product pages or contact your local sales representative and ask for a demonstration. We have a number of cards for evaluation that can run on the bench in boxes like the one shown above and can be pre-loaded with the operating system of your choice for short term evaluations.
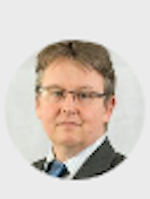