Extreme environmental situations: connector requirements for space electronics
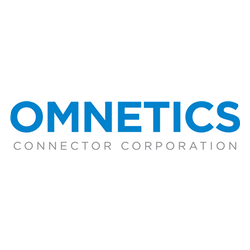
Space technology for electronic systems has evolved to meet the needs of long-range performance in extreme physical and environmental situations. From launch to deep space travel, the demands can be daunting, considering they cannot fail and cannot be repaired.
On August 6, 2015, the world sat still, quietly awaiting word of a Mars landing, and at 1:25 a.m. ET, the wait was officially over. “Curiosity,” the world’s largest object ever placed on Mars had finally emerged and begun its journey. As it sifted through the red dust of planet Mars, Curiosity was no longer a concept that many countries and researchers have tried and failed to create, but rather an engineering marvel thriving in one of the harshest environments one could imagine. Curiosity stands alone on many fronts. From the research and development stages to the seven minutes of terror, each component aboard had a distinct job to do.
CURIOSITY
Space technology for electronic systems has evolved to meet the needs of long-range performance in extreme physical and environmental situations. From launch to deep space travel, the demands can be daunting, considering that they cannot fail and cannot be repaired.
Omnetics provided over a dozen nano-miniature connectors used within two miniature inertial measurement units (MIMU) aboard Curiosity. These components played vital roles in terms of ensuring a safe landing for Curiosity on the red planet.
During launch from earth, the high shock and vibrations the craft experiences has a tendency to damage or stress standard electronic components. For example, connectors mounted on printed circuit boards must withstand potential sheering from the high G forces placed upon them. Since we all know that force is a product of mass times acceleration, designers often select connectors as well as other components to be small, lightweight, and of low profile. Mounting tabs and larger solder landing pads are also used in some applications.
Space-oriented electronic circuits drive a number of other connector specifications. Since the electronics themselves must not drain batteries quickly, many of the circuits require very-low voltages and low current flow to do their jobs. In addition, those circuits carrying digital images must carry massive amounts of data while sustaining high signal integrity to ensure image quality. To do this, the connector and cable systems must be matched carefully to the impedance of the circuits and avoid distortion or “holes” in the image base. Some lower-elevation satellites scan earth for images and process them at very high frame rates, like a high-speed movie camera. The differential signal process is highly dependent upon the connector and cables electronic design as well as the rugged reliability of the packaging.
For Curiosity, Omnetics connectors were used to support the spacecraft guidance and altitude control information sent back to the folks in mission control at NASA’s Jet Propulsion Laboratory. This particular aspect of the mission to Mars was vital in terms of ensuring a safe landing. Traveling at nearly 13,000 MPH leading into the final stages, Curiosity had less than seven miles during which to come to a screeching halt, and the SUV-sized rover certainly did not disappoint; neither did the components involved. This was Omnetics Connector Corporation’s second successful mission to Mars since 2008, with the Phoenix Mars Rover being the first.
Omnetics specifically selected materials for thermal-expansion match to sustain continued performance from the launch pad through geo-thermal orbit conditions. Materials were also used to ensure low out-gassing as temperatures varied significantly throughout the trip. Increased densification of the physical cable diameter and Nano-miniature connectors significantly helped reduce weight which led to lower payload costs. Special designs for unique cable requirements solved EMI, cross-talk, as well as high-speed problems. Connector backshells, strain-reliefs, braided shields, and specialty cables are also often used to improve handling and to extend the life of critical systems.
CONNECTORS FOR DEEP SPACE ELECTRONICS
For low weight and rugged space performance, some connector manufacturers have released spacegrade nano-D connectors. These MIL-DTL-32139 nano-miniature connectors are approved for space programs and inspected per EEE-INST-002.
Nano-D connectors, at .025” pitch, are the smallest space-grade connectors on the market; nano-D connectors have reduced size and weight by as much as four times that of standard micro-D connector and eight times that of previous D-sub footprints.
Better connectors use unique flex-pin gold-plated contacts that are polarized and shrouded by liquid crystal polymer insulators. The pin-to-socket strength and “lobed” housing alignment system makes these connectors capable of more than 2,000 mating cycles.
Space-grade connectors are available in a number of tail terminations. Standard pre-wired connectors come in 18”, 36” and 48” lengths with 80 microinches of silver-plated 30 AWG (7-38) PTFE insulated wire. Board-mount options include both surface-mount and through-hole variations. If you are using a flex circuit, flex tails are also available. Shell finishes include nickel-plated aluminum, stainless steel, and titanium.
Note: Cadmium plating and materials are prohibited for space applications. Pin-and-socket systems must be built and engineered to withstand the high shock and vibrational elements often associated with deep space exploration.
OUTGASSING
We’ve learned that both plastic as well as rubber materials give off gaseous molecules. In fact, the physical environment in which these components are used plays an even bigger role in terms of the immediate effect. Environments such as deep space feature both heat and vacuum elements, both of which increase the rate to which these gasses diffuse. In a spacecraft, these gases (produced by polymers) can become a legitimate problem, contaminating certain optical surfaces and instruments. The results can severely degrade the equipment’s performance.
The space world has adopted a standardized test procedure called ASTM E 595. The purpose of this test is to evaluate the outgassing properties of polymers. Within this test, small samples of materials are heated up to 125°C (257° F) at a vacuum of 5 X 10-5 torr for 24 hours. At that point, the sample is then weighed to calculate the total mass loss (TML). The TML cannot exceed 1.00% of the total initial mass. During this test, outgassed matter condenses on a cooled collector plate. This quantity of outgassed matter is calculated to determine the collected volatile condensable material (CVCM).
NASA SCREENING
The NASA specification EEE-INST-002 provides instruction on selecting, screening, and qualifying parts for use on NASA GSFC space projects.
Most space-certified connector companies offer NASA screening per EEE-INST-002. Table 2J in the NASA spec contains specific inspection instructions for nano-miniature connectors. These additional screening requirements exceed those set previously by MIL-DTL-32139 in terms of inspection levels. NASA defines three levels of screening: Level 1 for the highest level of reliability or for applications deemed mission-critical; Level 2 for high reliability; and Level 3 for standard reliability.
Space-grade connectors are often descendants of military-grade connectors. As new requirements are specified, connector design engineers use solid model software to modify the shells and mounting formats based on the specific application for the connector that will be used. Quick adjustment to existing designs can be done economically and fit into unique shapes and formats for the high shock, vibration, and long flight durations required. Specialty materials may be needed to protect the electronics inside the space box, as outgassing of some polymers can be detrimental to the electronics. Specifications and tests are routinely used to ensure the system is space-grade.