Military and aerospace requirements demand greater strength, speed, and capabilities in smaller form factors.
Aerospace and defense vehicles and electronics are shrinking in both size and weight, while system requirements continue to expand over time. Greater demands are being placed on increasingly compact platforms and systems, as a wealth of military and aerospace applications move to small-form-factor (SFF) embedded computers.
SFF computing technologies benefit narrow, pod-mounted data collec-tion systems. (Photo: U.S. Navy/Mate 3rd Class Shannon R. Smith.)
Across the board
The applications for small form factors are not trending to one market, U.S. Department of Defense (DOD) service, or application type, explains Doug Patterson, vice president of the military & aerospace business sector at Aitech Defense Systems in Chatsworth, Calif. "Applications for SFF are seeing near equal adoption for air, land, sea, and space, manned or unmanned/robotic."
Commercial aviation applications for SFF computing also abound, throughout passenger jets, air traffic control towers, and airport runways. "One application for SFF is the robotic automation of commercial aircraft tugs," Patterson says.
Israel Aerospace Industries' (IAI's) TaxiBot semi-robotic, pilot-controlled vehicle transports commercial airline aircraft from terminal gates to the runway and back without using the airplane's engines. The main tug mission computer is a SFF Intel Core i7 stand-alone computer with eight CameraLink frame grabbers for spatial imaging and image/obstruction recognition, Patterson describes. On the military side, he adds, various unmanned aerial vehicles (UAVs, also known as unmanned aircraft systems or UAS), unmanned ground vehicles (UGVs), and unmanned underwater vehicles (UUVs) rely on SFF computers, given their small size.
SFF for SWaP-constrained apps
Aerospace and defense computing platforms have always had significant space, weight, and power constraints, says Mike Schneider, vice president of business development, sales, and marketing at Mercury Systems - Trusted Mission Solutions group in Fremont, Calif.
"Over the past several years, however, more functions are being automated and application software performance requirements are growing even more quickly," Schneider explains. "Not only do these factors add up to increasing demand for SFF embedded computers, but also for SFF computers that pack more performance into increasingly smaller packages. All this additional capability must still go into the same space- and power-constrained aerospace defense platforms."
Engineers are under pressure to provide SFF computers with greater functionality in the same or less space than currently fielded systems - and they face several engineering design challenges, including power and thermal management.
"More performance in more and smaller form factors puts a premium on striking the right balance between performance and cooling," Schneider says. "Furthermore, these SFF systems must survive on platforms that endure extreme environmental conditions that include shock, vibration, heat, cold, humidity, etc. This presents great opportunities for thermal, kinetic, mechanical, and electrical engineers to collaborate on innovative solutions to exceptionally difficult systems engineering challenges faced throughout aerospace and defense."
Enterprise-level computing
The demand for SFF in aerospace and defense is driven by the need for high compute capabilities in SWaP-constrained applications, observes Dave Caserza, embedded computing architect at Elma Electronic Inc. in Fremont, Calif. "The market is demanding that high-end, modern desktop technology be made available to deploy in harsh embedded environments. Such technology typically means applying high-speed sensors to large graphics processing units (GPUs) and field-programmable gate arrays (FPGAs).
Aitech Defense Systems' A176 rugged GPGPU system incorporates the NVIDIA Jetson TX2.
"The biggest challenge is the thermal design and the ability to package 150 watts or more in a small, sealed, fanless box that has to operate over a very broad temperature range," Caserza admits. "For example, an avionics application might be fine running at 30,000 feet or higher, but then it also needs to run on the tarmac in the desert."
Mercury Systems' Schneider agrees that the greatest engineering challenge in SFF computing is thermal management. "When designing and implementing SFF solutions, it is important to choose innovative partners with deep expertise in size, weight, power, and cooling optimization across a wide range of form factors specifically designed for mission-critical applications," he says. "By utilizing the latest contemporary technologies, these leaders can deliver the highest performance in the smallest possible package without sacrificing reliability."
3U from 6U
Traditionally, 6U has been the standard form factor for a majority of commercial off-the-shelf (COTS) electronics in aerospace and defense. Technology refresh is enabling miniaturization, making the 3U form factor a popular choice.
"You can now get on a 3U board what used to take multiple 6U boards," says Aaron Frank, product manager, COTS Solutions at Curtiss-Wright Defense Solutions in Ottawa. "3U is better than 6U from a thermal-management perspective because components are almost always closer to an edge and, in a conduction-cooled environment, the closer you are to the edge of the board, the better the thermal cooling solution."
Curtiss-Wright OpenVPX and XMC processor modules are tailored to aerospace & defense.
Frank is seeing increased demand for 3U designs across the board, but primarily in ground and air environments. "Where they used to have one box that handled single or dual functions, they now have the need for many more functions onboard a single platform," he says. "For that reason, customers are trying to consolidate space, and put many different pieces of equipment in the same space where a single- or dual-function box used to reside. That's helping to drive smaller-form-factor boards and packaging to meet those needs.
"A perfect example of being able to do more with 3U today, Curtiss-Wright was successful in designing a 3U board that had all the functionality of two to three 6U boards in a 3U space by taking advantage of advances in microelectronics, miniaturization, and the latest printed circuit board (PCB) design rules and technologies without sacrificing any performance or reliability of an extremely rugged design," Frank describes.
"The board uses an XMC mezzanine card that packs all the punch of what's also integrated on the 3U host," Frank says. The XMC card can be added to any existing 3U board to double the performance and functional density. "In other words, the power of two 3U cards can be put into a single slot using this XMC approach." The design helped Curtiss-Wright win first place in the military and aerospace design excellence category at the 27th Annual PCB Technology Leadership Awards by Mentor, a Siemens Business.
Small size can bring power benefits, recognizes Mike Southworth, product manager at Curtiss-Wright Defense Solutions in Salt Lake City. A platform may have constraints because of the payloads onboard, he says. "In the case of a platform with an intelligence, surveillance, and reconnaissance (ISR) mission, there may be a number of sensors onboard and networks for Ethernet and processors that are taking data from the sensors and doing something with that data."
The smaller the onboard computers can be, the better, Southworth says. "It is to the advantage of the platform because it reduces the demands for fuel, enabling longer flight times if the platform is an aircraft, or extend battery life if it's a ground or surface vehicle. That can translate into lower power consumption as well, because you're dealing with smaller devices. So there are benefits from a power-management standpoint.
The Nanopak i7 rugged SFF system uses the Intel Core i7.
"The caveat is that the smaller [a system gets], the more concerned you should be about thermal management," Southworth continues. "The performance often needs to be balanced against what you can effectively cool. So there is a tipping point as far as what thermal management can do based on the performance out of the box."
Scalability and I/O flexibility
A significant challenge is finding SFF systems with flexible input/output (I/O) options that address the wide range of I/O required on today's aerospace and defense platforms, Mercury's Schnieder points out.
"The smaller the form factor, the less backplane slots and less I/O interface capabilities in terms of how many additional cards that can be integrated into the I/O architecture," Curtiss-Wright's Southworth says. SFF standards for I/O cards provide some level of flexibility, he adds, noting that PCI Express or PCIe-104 standards-based I/O cards are fairly small and enable the integration of a considerable amount of SFF functionality.
At the same time, Southworth says, "the interconnect building blocks for signals inside and outside of SFF systems are being miniaturized, allowing us to shrink the footprint of the box. Often, in the past, the size of the box was driven by the connector's shell size and now there's miniaturized versions of the most popular military connector types - that allows those boxes to shrink in size."
With SFF subsystems, it's easier to break the solution into multiple boxes, placing the processing in one box and the I/O in another, for example, says Curtiss-Wright Defense Solutions Chief Technology Officer (CTO) David Jedynak in Austin, Texas. "That way you can avoid having to have all the I/O in a single box. Instead of having one box that has the entire 'kitchen sink' in it, doubling the I/O and increasing the unit size and connector counts, you can achieve benefits by going with multiple SFF units."
Cost benefit with caveats
SFF embedded systems generally cost less than a bus- or fabric-based, board-level integrated system that is equivalent in functionality, Patterson explains. "More functions can be packed and split onto less internal boards, meaning there are fewer internal printed wiring boards (PWBs), no backplane, fewer inter-board connectors, etc."
The drawback, Patterson cautions, is trading potentially lower upfront costs vs. future modularity - sacrificing the ability to add functionality at a later date, when platform requirements change, when memory (or other functionally) needs to be expanded/added, or when component obsolescence demands the SFF internals be redesigned, instead of isolating the change to only one industry-standard board.
Scalability is an ever-present concern, as engineers struggle to expand the features and functionality of already maximized SFF devices. "At the moment, you have these small systems on one end of the scale, and 3U/6U module-based systems at the other end," describes Mark Littlefield, technical product manager, defense at Kontron, an S&T company, in San Diego. "There is a dip in the capability/cost space between the two where the system needs exceed the capabilities of a SFF system, but the costs of a board/chassis-based solution is unattractive for the relatively small size of the system. We are looking at ways to bridge this gap."
Density by design
The advantages of SFF embedded computers are predictable: size, weight, and power (SWaP); they also cost less than bus-and-board-type plug-in modules, says Chris Ciufo, chief technology officer at General Micro Systems (GMS) in Rancho Cucamonga, Calif.
"An SFF system has the advantage of being completely self-contained and built using inherently low-cost, commercial off-the-shelf (COTS) technology," Ciufo says, "and it's highly optimized for solving a particular system-level problem while meeting or exceeding tough environmentals." For example, the company's SFF, conduction-cooled, Windows 10 Pro system can drive three 4K-resolution (3840 x 2160) UHD video displays and includes MIL-STD-1553 plus multiple Ethernet local area network (LAN) ports - yet, it uses roughly 60 watts of power, he says. "The box is about the size of a half-carton of eggs, but is so robust you could park a truck on top of it without any damage to the box. It's hard to beat that kind of super-dense functionality."
"SFFs are in great demand by military applications that don't have a lot of space," Ciufo continues, "particularly fighter aircraft and UAV/UAS platforms. SFFs are obviously small and can be tucked into all kinds of available spaces in airframes, vehicles, and other platforms." If you can cable up to it, you can add new functionality, he says.
The small size and purpose-built functionality of a SFF system resonates well with airborne platforms, Ciufo says, estimating that GMS's biggest growth market is designing server-based SFFs into airborne systems. "These are the kind of applications that demand server-class performance with cloud-like connectivity - via satellite communications (SATCOM) or local database storage - but absolutely cannot afford the size and power you get with a rack-mount server."
Space-based applications are a growth area ideally suited for SFFs but aren't particularly high-volume, Ciufo says. "In space, the SFF is highly customized to fit the power budget of a solar-powered platform, and the size and weight constraints needed for spacecraft." Nothing excess is added in a space-based SFF, he adds.
The Systel EB7001 is a rugged SFF video-capture solution for mission-critical operations.
Vehicle networks
The advent of multi-core, system-on-chip (SoC) processors have made it possible to build very capable computing platforms with very small footprints, Kontron's Littlefield says. This has, in turn, led the defense community to look for ways to apply these new products. "In addition, many problems that required multiple processors to solve can now be handled by a single multi-core processor. As a result, SFF is becoming more attractive to a wider set of defense system designers."
Kontron leverages its SFF modules used in the industrial, medical, and commercial computing spaces to create very compact, deployable mission computers designed to be easily modified to meet a particular mission's requirements. It is the logical basis for the company's COBALT, TRACe/EvoTRAC, and KBox product lines, Littlefield adds.
"Both the civilian and military avionics markets are really attracted to COBALT. Having an easily-customizable tightly-packaged fanless mission computer is quite useful for these types of systems," Littlefield explains. "We're also seeing a lot of interest in the military ground vehicle segment, mainly because small systems like this easily bolt into the odd corner of a vehicle and quickly integrate into the vehicle's network."
Kontron's COBALT 901 rugged embedded platform is used in Hughes Network Systems' HM200 compact, low-power Comms-On-The-Move (COTM) SATCOM modem for a wide range of deployed defense or commercial environments. "We took our standard, off-the-shelf COBALT and created a custom bottom plate to mount the Hughes Satellite Modem board, created a cable to connect the modem board to the rest of the COBALT system, and modified the front panel to bring out the RF connectors," Littlefield describes. "It was really that straightforward.
"SFF boards and systems are an attractive solution for a broad range of applications, and should be added to every system integrator's toolbox," Littlefield says.
Net-centric C5ISR
Network-centric warfare is driving the demand for innovative, rugged SFF embedded computers, says Aneesh Kothari, vice president of marketing at Systel in Sugar Land, Texas. Space is at a premium and aerospace and defense platforms are consolidating and becoming more compact.
"Modern missions are increasingly focused on intelligence, surveillance, and reconnaissance (ISR), necessitating multifunctional computing systems with dense computing and robust capabilities," Kothari explains. "The major benefit of SFF embedded computers is hardware consolidation. Single line replaceable units (LRUs) can take the place of multiple legacy systems, resulting in significant savings in price and SWaP, not to mention vendor management and support."
The Crystal Group RE0412 rugged embedded computer is housed in a carbon-fiber chassis.
Thermal design becomes critical, and innovative design is key to dissipate heat from high-performance, high-wattage boards and modules, Kothari continues. "Systems without moving parts are desirable in many aerospace and defense applications, eliminating reliance on convection cooling using fans to blow air through the system." Expertise in system engineering and thermal design is critical, particularly when military requirements call for sealed systems and use in harsh environmental conditions.
Kothari describes Systel's rugged SFF embedded computers as multi-mission solutions "providing an economy of capability within a superior SWaP-C optimization effort." Systel's SFF mission systems are used in command, control, communications, computers, combat systems, intelligence, surveillance and reconnaissance (C5ISR) applications - including airborne ISR, counter unmanned aerial systems, persistent surveillance, law enforcement, border security, and search and rescue - providing "the warfighter with a multi-capable LRU supplying a single point for all sensor ingest, processing, mission software management, storage of all critical data, and network distribution."
Airborne ISR
SFF computers in miniATR form factors are being mounted in mobile ground vehicles for command, control, communications, computers, intelligence, surveillance, and reconnaissance (C4ISR) and imaging/sensor applications, Elma's Caserza says. "We're also seeing the implementation of SFF computing platforms using the COM Express form factor, particularly in mobile computing applications. This platform offers high I/O configurability, without designing from scratch."
In defense, the greatest demand is in UAVs and ground vehicles due to the SWaP constraints in those applications, Caserza affirms. "New and emerging COM Express and PCI/104 high-performance CPU products are making it possible to use those architectures where previously only a slot-card-based Eurocard system was considered."
ISR innovation
SFF enables much more intelligence to be added to platforms that previously would have had very little onboard, Curtiss-Wright's Jedynak explains. "For example, smaller deployed platforms, like UAVs, which didn't previously have the ability to host significant amounts of processing, now can. Customers see that smaller, more powerful rugged computers are now available, and that's encouraging them to think of innovative ways to use and deploy them."
New types of smaller platforms that didn't exist before are helping to drive demand for SFF, such as UAVs designed for use in swarm applications, Jedynak says. "That type of application was not possible before the emergence of the new classes of SFF embedded computers and network switches."
Autonomous vehicles
One of the newest high-growth areas for SFF computing is autonomous vehicles (AVs). "A wide variety of automated systems are required to create an autonomous vehicle capability," Mercury's Schneider says. Other growth areas include so-called "smart" functions, such as automated inventory management, vehicle health management, and smart security systems, he says.
Mercury Systems' NanoPak i7 SFF systems are used in an Internet of Things (IoT) application on an unmanned vehicle. "It is an entry point for raw data, enabling data preprocessing and reduction to optimize transmission over bandwidth-constrained networks," Schneider describes. "Other applications include a virtual console capability, essentially a thin client in a virtual desktop infrastructure application. Our rugged tactical switches, which include an internal embedded shared processor, not only provide networking capabilities on Army tactical vehicles, but also host network services software used by other systems on the network."
Rugged computer and electronic hardware designer/manufacturer Crystal Group in Hiawatha, Iowa, is seeing increased demand for its small-footprint, rugged computers in autonomous, airborne, shipboard, vetronics, and other critical applications, including missile defense.
Missile defense
Growing global tensions and threats have all eyes on missile defense. The U.S. defense budget request for fiscal year 2019 calls for investments in layered missile defenses and disruptive capabilities for both theater missile threats and ballistic missile threats.
Crystal Group engineers designed compact, rugged computer systems for two major components of the U.S. missile defense network and strategy: the U.S. Army Integrated Air and Missile Defense (AIAMD) and the Integrated Air and Missile Defense Battle Command System (IBCS).
The AIAMD system enables the integration of current and future modular components in a network-centric, plug-and-fight architecture to exploit the full combat potential of air and missile defense capabilities on the battlefield. AIAMD takes advantage of the Crystal Group RS112 1U Rugged Server for its flexibility, scalability, robustness, and rugged environmental performance. Similarly, the IBCS establishes a network-centric system of systems that integrates current and future air and defense systems to maximize defense capabilities, optimize resources, and provide flexibility on the battlefield.
Ruggedization is a requirement for missile defense and a growing number of other SFF applications. "Don't get seduced by solutions that weren't designed from the ground up to operate in the harsh environments typical of military and aerospace applications," Southworth cautions. "Not all SFF computers are designed equally. Select SFF solutions that are qualified to the types of rigorous requirements typical of deployed platforms."
COMPANY LIST
AcroMag
Wixom, Mich.
https://www.acromag.com
ADLINK Technology
San Jose, Calif.
http://www.adlinktech.com
Aitech
Chatsworth, Calif.
http://www.rugged.com
Chassis-Plans
San Jose, Calif.
http://www.chassis-plans.com
Core Systems
Poway, Calif.
https://core-systems.com
Crystal Group
Hiawatha, Iowa
https://www.crystalrugged.com
Curtiss-Wright
Ashburn, Va.
http://www.curtisswrightds.com
Diamond Systems
Sunnyvale, Calif.
http://www.diamondsystems.com/
Ecrin
Crolles, France
http://www.ecrin.com/en
Elma Electronic
Fremont, Calif.
http://www.elma.com
Extreme Engineering Solutions Inc.
Middleton, Wis.
https://www.xes-inc.com
General Micro Systems (GMS)
Rancho Cucamonga, Calif.
https://www.gms4sbc.com
Kontron
Fremont, Calif.
https://www.kontron.com
Mercury Systems
Andover, Mass.
http://www.mc.com
Sparton Rugged Electronics
Woodbridge, Ontario
https://www.spartonre.com
Systel
Sugar Land, Texas
http://www.systelusa.com
Technology Advancement Group (TAG)
Dulles, Va.
https://www.tag.com
Themis Computer
Fremont, Calif.
https://www.themis.com
V Rose Microsystems
Johnstown, N.Y.
http://www.vrosemicrosystems.com
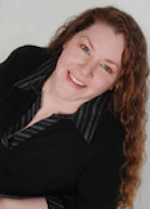
Courtney Howard | Executive Editor
Courtney, as executive editor, enjoys writing about all things electronics and avionics in PennWell’s burgeoning Aerospace and Defense Group, which encompasses Military & Aerospace Electronics, Avionics Intelligence, the Avionics Europe conference, and much more. She’s also a self-proclaimed social-media maven, mil-aero nerd, and avid avionics geek. Connect with Courtney at [email protected], @coho on Twitter, and on LinkedIn.