NASHUA, N.H. -Â Power electronics has come a long way since its dominance several years ago by discrete power devices and esoteric design approaches that usually required close involvement from experienced power engineers.
Nowadays power electronics is entering the realm of systems integration by combining with high-speed networking, microprocessors for smart power designs, and innovative approaches for thermal management to help keep electronics cool.
Power electronics — the control and conditioning of electrical power for ever-smaller and more sensitive electronics components — is following technology trends in power density and small size, weight, and power consumption (SWaP); innovative cooling and thermal management; adherence to open-architecture industry standards; high levels of systems integration; obsolescence management; and a reliance of commercial off-the-shelf designs.
Power density
“We operate in three different markets: North America, Europe, and Asia,” points out John Imaz, vice president of sales and marketing at power electronics specialist Gaia Converter in Le Haillan, France. “The common denominator is an increasing need for high density and efficiency. SWaP is the most common trend we are seeing. We are trying to get as much power density in the smallest possible package with good thermal performance.”
Providing ever-more power in small power electronics packages is a challenge that all power electronics companies face when serving the aerospace and defense market. “I see remote-control drones for military and civil applications that have been driving some of these weight challenges,” Imaz says. “VTOL [vertical takeoff and landing] is coming up as the next big trend in commercial aerospace power.”
Also driving power density in these kinds of devices are electric vehicles and aircraft, Imaz says. “We are trying to get closer to the electric motor, so when youOne of Gaia’s biggest customers, a European aircraft designer, is considering hydrogen-power propulsion as one way of driving the electronification of the entire airplane, Imaz says. In applications like this, small size and light weight can spell the difference between a successful or an unsuccessful design. The same rules apply to satellite designs — also a growing driver in power electronics technologies.
“Our customers are asking for us to get them power devices that are very small, very light, very high performance, and long-lasting capacity — all at a more competitive price point,” Imaz says. Amid intense competition among systems integrators, “we need to make sure money is used wisely, Imaz says. “Our customers need availability and performance, and a competitive edge.”
The need for power density runs across the board — especially for military applications, says Howard Schrier, vice president of marketing at Nova Electric in Bergenfield, N.J., an autonomous division of Technology Dynamics Inc. (TDI). “Everybody wants smaller and lighter; that’s what the military wants,” Schrier says.
Nova Electric offers rugged solid state frequency converter systems for military, industrial, and commercial applications, and can build to military environmental and electrical standards such as MIL-STD-810, MIL-S-901, MIL-STD-167, MIL-STD-1399, and MIL-STD-461. Nova’s frequency converters come in rackmount, freestanding, or wall-mount NEMA cabinet versions, as well custom enclosure configurations.
Space power
Space “is a very exciting market, and our customers need high-density power,” says Rob Russell, vice president of product marketing at Vicor Corp. in Andover, Mass. Vicor specializes in high-reliability DC-DC converters for radar, vetronics, and satellite applications.
Vicor traditionally provides power electronics for terrestrial military, industrial, and commercial applications, and is expanding into the so-called “new space” market for affordable radiation-tolerant power converters.
In January Vicor announced the launch of the company’s first radiation-fault-tolerant DC-DC converter power modules aboard the Boeing Co. O3b mPOWER satellite, part of a constellation for telecommunications and data backhaul from remote locations. The satellites will operate in medium-Earth orbit.
Vicor’s power electronics devices aboard the satellites are housed in the Vicor plated SM-ChiP package, and can power low-voltage application-specific integrated circuits (ASICs) with as much as 300 Watts from a 100-volt nominal power source.
Boeing tested the Vicor’s power devices to resist the effects of 50 kilorads of total ionizing dose radiation, and to be immune to single-event upsets using a redundant architecture in which two identical and parallel powertrains with fault-tolerant control circuitry operate in one high-density package.
Thermal management
There’s a potentially damaging byproduct of shrinking power devices while increasing their capacities: heat. As such, thermal management and electronics coolingTake military ground vehicles, which are expected to operate in some of the world’s hottest deserts, where electronics temperatures can soar — especially in tightly packed electronics systems. “In ground applications like armored vehicles, operating temperatures are becoming critical issues,” says Gaia’s Imaz. “Electronics must operate in harsh environments where temperatures are critical.”
Applications like these are where new and emerging open-architecture industry standards — developed originally for new generations of high-performance embedded computing — are coming into their own.
“Conduction cooling designers are starting to consider other modes of cooling than conduction,” says Brian Paul, general manager at power specialist MilPower Source in Belmont, N.H. Still, an expertise in thermal management, as well as in power density, can help power electronics companies gain a competitive edge in their markets.
MilPower designers are starting to use VITA industry-standard VPX Air Flow-By cooling for some of their products, Paul says. “We are seeing much more of an Air Flow-By cooling trend in our industry. We are offering our M4706 three-phase AC input device with holdup. It also provides 1,100 Watts of power in a VPX power supply. This helps integrators separate themselves from their competitors.”
Industry standards
One substantial trend in power electronics technologies today is adherence to open-architecture standards like VITA OpenVPX and the Sensor Open Systems Architecture (SOSA) standard. “More and more, system-level solutions are using common standards,” says Gaia’s Imaz. “We do see that requirements are somewhat different in our different markets, but we need to make sure our products are compatible with the largest number of standards.”
Moving toward standard products and away from custom products also has other implications, Imaz explains. “It’s a trend to move away from the traditional role of a power engineer, and more of a shift to project managers who are looking for ready-to-use solutions that meet common industry standards.”
Open-systems standards are becoming part of the landscape in power electronics, as they are in embedded computing and other technologies. “A big trend is open-architectures, and how open architecture standards are impacting systems designs,” says MilPower’s Paul. “We are seeing a lot of engagement from industry in minute detail of how to put together power-management solutions. Industry must operate under mandates for open architectures.”
MilPower is offering the company’s M4162 one-inch-pitch power holdup module that is designed to align with SOSA requirements, Paul says. “Everybody is trying to do something unique and different, yet stay in open architectures.”
The SOSA standard, itself, is helping power systems designers come up with new designs to meet evolving customer demands. “We have heard from customers that the 28-volt bus has no more capacity. With SOSA, if you want something that takes more power, there is a 270-volt bus that is available. We are seeing that on legacy aircraft. It provides SOSA solutions to meet that need.”
Vicor experts see enough importance in SOSA standards to join with the SOSA Consortium, which is under aegis of The Open Group in San Francisco. “SOSA is another coming trend,” says Vicor’s Russell. “There are many more designers today who want that technology, and I see that being a clear-cut trend that is happening now.”
Systems integration
In a growing number cases, it’s not enough simply to provide power supplies; instead, customers are asking power companies for more, such as networking capability, smart power systems, and the like. As a result, companies that at once time specialized in power devices alone are moving up the food chain to offer integrated systems with plenty of added value.
“Our customers are asking for an off-the-shelf integrated solution,” says MilPower’s Paul. “The trend is integrated solutions make a lot of sense.” MilPower is adding networking capability to its lines of power devices for remote control and smart power systems that use artificial intelligence (AI). “Yesterday we might have had to partner with someone, but now we have an integrated solution, and it is a lot easier to day. it’s more subsystems integration to more features into one box that makes sense.”
The need for systems integration at the subsystem level is one reason for power company mergers and acquisitions over the past several years. “Companies areWhen it comes to integrating power and networking capabilities, Paul says MilPower is carving-out a seldom-served niche. “Nobody has really served that market by integrating power and networking products from the ground-up for military applications. Integrated systems also are attractive because there rarely is money for non-recurring engineering (NRE) for custom products. “Industry has to be willing to get the right capability out to the warfighter,” he says.
Gaia’s Imaz says he also is seeing customer demand for integrated products rather than stand-alone solutions. “There is more demand now for what is more than just a modular solution,” he says. “More of our end-customers and the primes are asking for more of a complete power supply unit [PSU] solution.”
Power companies also view integrated systems as pathways to designing-in artificial intelligence and high-end microprocessors, graphics processors, and digital signal processors for smart power systems of the future.
“Artificial intelligence is another key driver,” says Vicor’s Russell. “It will require a whole other level of power control, and we have the premiere product capability for those kinds of high-current graphics-processing units and application-specific integrated circuits.”
Obsolescence management
“While you are replacing an obsolete part or diminishing manufacturing source, you can add more for the warfighter,” says MilPower’s Paul. “If you do it right you can bring a lot of value to the user.” MilPower engineers used this approach in a recent contract involving a U.S. Army infantry anti-armor weapon. By blending-in new technologies to obsolescent power electronics subsystems, MilPower was able to reduce the size of a battery charger from 148 pounds to about 30 pounds.
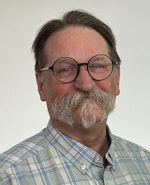
John Keller | Editor-in-Chief
John Keller is the Editor-in-Chief, Military & Aerospace Electronics Magazine--provides extensive coverage and analysis of enabling electronics and optoelectronic technologies in military, space and commercial aviation applications. John has been a member of the Military & Aerospace Electronics staff since 1989 and chief editor since 1995.