Electric power control and conditioning for ever-more-powerful and -complex embedded computing processors, sensors, RF transceivers, and other advanced components poses challenges today that involve size, weight, and power consumption (SWaP); efficiency; thermal management; new materials; ruggedized packaging; and the growing influence of open-systems industry standards.
It's one thing to design microprocessors that are smaller and more powerful with each passing year, but it's quite another to design the kinds of DC-DC convertersSystems integrators are looking for power electronics technologies that can help them enhance efficiencies to help them reduce size and weight; meet the guidelines of open-systems standards when they're specified; manage internal heat, accommodate advanced materials, and design for harsh environments that involve shock, vibration, and temperature extremes in next-generation radar, electronic warfare (EW), rugged computers, and similar systems.
Shrinking size and weight
Trends in the power electronics market mirror those of many other segments in the electronics industry: everything's getting smaller. This shrinkage of electronic components is fueling aerospace and defense electronics trends in unmanned vehicles, surveillance and reconnaissance, avionics, communications, and many other applications.
"Everything is shrinking in size," says John Santini, chief technology officer of Micross Components Inc. in Melville, N.Y. "Everybody is looking to do point-of-load regulation closer to the ICs -- especially ASICs and processors. It gives you much better transient response, and you don't have conductive losses in the traces, and you save board real estate."
Some power electronics companies are shrinking device size by increasing the level of integration of their products. One such company is Gaia Converter in Bordeaux, France. "We offer a complete range of products that are 8 millimeters tall for use in VPX systems where you don't have a lot of space," says Christian Jonglas, Gaia's technical support manager.
"This year we started to compress functions into one module," Jonglas continues. "This is a trend today at Gaia Converter to embed all power functions on one device. We are developing the FLHG 60 DC-DC converter, which includes all front-end functions you need to place in front of the DC-DC converter."
Gaia's power integration efforts continue. "In the future we will put a complete power supply in one COTS [commercial off-the-shelf] case," Jonglas says. Gaia's PSDG 40 -- a 40 watt power supply -- will be introduced later this year, which will be a complete power supply in one COTS module, with four to five different power outputs, Jonglas says. This product should be compliant with DL 160 and MIL STD 461.
This trend in power systems integration has been a long time in coming. "In 2005 we were doing 150 Watts in a half-brick module, and today it is 500 Watts," Jonglas explains. "We will be at more than one kilowatt in one-half brick, and this should be ready very soon."
Another way to reduce SWaP is to move to advanced materials like gallium nitride and silicon carbide, instead of traditional silicon MOSFETs. "The size of a GaN FET, compared to a silicon MOSFET, is about an eight times reduction in volume," says Brian Paul, general manager at Milpower Source Inc. in Belmont, N.H.
Couple that reduction in SWaP to the increased performance of GaN and SiC FET. "Designers get the temperature range they need, and we are pushing beyond 800 Watts in a 3U VPX power supply now," Paul says. "We started building 3U VPX power supplies in 2015, and since then we have moved from about 250 Watts to beyond 800 Watts, due to the materials and the innovation of what you can do in that volume. we also do discrete component designs, which enables you to stuff more in the same volume."
Designing for power efficiency
Efficiency in a power supply is the ratio of total output power to input power, expressed in percent, and represents the amount of the actual power delivered to the components divided by the electrical power drawn from the supply socket. The better the efficiency, the more power goes to good use, and the less power goes to waste heat. It's a primary goal among power supply designers to make their devices as efficient as possible.
"The number-one change that we've seen in the past several years is efficiency," says Jeremy Ferrell, director of engineering at VPT Inc. in Blacksburg, Va. "People are changing what their efficiencies are, and are pushing that down to the power converter. Every little bit of power they can save is a big reduction in weight from solar panels and batteries. Our customers are demanding more efficiencies."
The demand for efficient power never seems to end. "Customers always want more efficiencies," Clauson says. "Our customers will do things like drive higher voltages; they are looking for more, and more power at the same voltages. The way to go is to higher voltages to make up for higher copper loss."
For Rantec and other power electronics designers, the trend is clear. In 3U VPX power supplies, for example, in recent years were able to supply 500 Watts, and that has grown to 750 Watts -- all in the same-sized package, Clauson says.
New industry-standard power designs are pushing for higher efficiencies. "In our VPX VITA 62 power supply, the standards accommodate 3.3 and 12 volts, but now they just want more power at only 12 volts," Clauson says. "For customers that simplifiers their design; they don't have to deal with three different voltages, and can route more power on the backplane because they have a higher voltage. There is not as much current flowing through a backplane."
Increasing voltages "allows the system-level designer to have more power available, and from a power supply perspective he can get higher system level efficiencies by not using those 3.3 power voltages; the whole push for going in that direction, is doing things they haven't been able to do before, Clauson says. "They can add more and more capability to these military platforms, such as computing, radar, and CNI/EW [communications, navigation, identification, and electronic warfare]. Everything is going to require more power electronics."
Integration also is the name of game at Micross for enhancing power efficiency. "We are developing solutions for the downconverter -- a large centralized architecture -- and at developing points of load sitting next to the processors," explains Lass Pedersen, vice president of the Micross high-rel power solutions segment in San Jose, Calif.
"With higher voltage, you get better efficiency in the whole system," Pedersen continues. "The higher voltage drives a need for less losses in output stage. As the transmitter is often the mission, and the mission always get most of the power, so the customer looks at the best efficiency he can get."
New device materials
Increasing voltages isn't the only way to enhance power efficiencies. Another way is to move beyond traditional silicon-based metal oxide semiconductor field-effect transistors (MOSFETs) and gallium arsenide (GaAs) to gallium nitride-based FETs or to silicon carbide (SiC). "We are using gallium nitride FETs, which represent a game changer," says VPT's Ferrell. "GaN can switch a lot faster than silicon. A lot of research is going into GaN, which is naturally radiation hardened,GaN represents a major trend for many power electronics applications. "At VPT we think GaN is the future as far as performance is concerned. There always will be a place for MOSFETs. We have spent the past eight years to make sure the circuits work reliably. There is a learning curve, and we are over that learning curve, but there is a pretty large boundary to enter that market."
Silicon carbide also is making inroads to power electronics technologies. "We see a lot of use of silicon carbide and gallium nitride to drive efficiencies," says VPT's Clauson. "These new ICs support addition efficiencies, and smaller dies."
Sometimes the application helps determine the choice of materials for power electronics devices. "Already now gallium arsenide is a niche for lower frequencies, while GaN is more popular for higher frequencies," says Pedersen of Micross. "Most likely GaAs will remain for niche applications."
The move to GaN should be a major boost to the power electronics industry, says adds Santini of Micross. The move to GaN also has helped the power conversion industry because now the buzz word in power conversion is to go to GaN and to silicon carbide. Those new technologies allow smaller and more efficient devices. GaN is really doing that on the low-voltage devices of less than 100 volts, and for devices of more than 100 volts silicon carbide is more popular."
Next-generation DC-DC converter power supplies also should benefit from GaN, which "is being optimized for switching power applications and for next-generation DC-DC converters," Santini says. "GaN lets you switch efficiently at high frequencies, and by moving the frequencies up, all the magnetics shrink, and you get better efficiencies."
Yet as new technologies come online, systems designers often face a new set of issues. "GaN opens up the box to a new set of tradeoffs," Santini says. "It decreases switching losses, and they allow the magnetics and capacitors to shrink as well, which drives smaller package sizes."
Flexibility in design is another advantage of switching to new materials like GaN and SiC. We have implemented GaN FETs, and use a lot of silicon carbide," says Milpower Source's Paul. "Silicon carbide is good at some of the higher voltages, and GaN can give you advantages in the lower voltages."
Power electronics applications
There are many aerospace and defense applications that are helping to push power electronics technologies forward. "At the end of the day the power electronics is driven by the application," points out Pedersen of Micross. "We do power because it is needed for different applications; wherever the applications are going, the power goes with them."
Pedersen says he sees four major trends driving developments in power electronics. "One is the increased need for processors. We see processors all over theThe second trend involves RF and microwave communications. "We are seeing increased bandwidth for communications," Pedersen continues. "One way to get that is apply higher frequencies in your communications systems, and there gallium nitride pushes things to higher frequencies. GaN is coming into the market as preferred technology. Pushing a need for instead of gallium arsenide transmitters that operate in 6 to 10 volts, but GaN transmitters are operating at 30 to 50 volts."
The third trend involves moving to higher voltages. "Higher voltage gets you better efficiency in the whole system," he says. "The higher voltage drives a need for less losses in output stage. The transmitter is often the mission, and the mission always gets most of the power, so the customer looks at the best efficiency he can get." The fourth trend involves applications in orbiting satellites, which requires some level of radiation hardness or radiation tolerance in power devices.
Other applications driving power electronics technology forward include unmanned vehicles with multisensor payloads, says Gaia's Jonglas. "You need power for all electronics inside -- cameras, sensors, all the systems of different voltages and power." Echoes VPT's Ferrell, "Target applications are any kind of transmitter, many with high-voltage output, but in any geosynchronous satellite."
Vast increases in the use of microprocessors in aerospace and defense systems across the board is a huge driver in power electronics innovation, says Milpower Source's Paul. "The amount of data they are crunching requires more and more power," he says.
More information on data storage manufacturers and suppliers is online at https://www.militaryaerospace.com/directory/components-power-electronics-sensors.
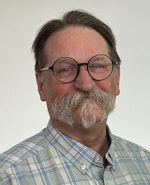
John Keller | Editor-in-Chief
John Keller is the Editor-in-Chief, Military & Aerospace Electronics Magazine--provides extensive coverage and analysis of enabling electronics and optoelectronic technologies in military, space and commercial aviation applications. John has been a member of the Military & Aerospace Electronics staff since 1989 and chief editor since 1995.