While summer is coming to a close, those in the electronics industry experts often have heat at the front of their minds. Engineers have the unenviable task of taking today's ever-more-powerful advanced components like processors and sensors and fit them into shrinking enclosures, all the while keeping everything cool.
Those increasingly diminutive electronics are enabling greater capabilities from all manner of technologies used in the aerospace and defense industries.
"Everything is shrinking in size," says John Santini, chief technology officer of Micross Components Inc. in Melville, N.Y. "Everybody is looking to do point-of-load regulation closer to the ICs -- especially ASICs and processors. It gives you much better transient response, and you don't have conductive losses in the traces, and you save board real estate."
While engineers work to reduce wasted energy, the nature of power electronics and physics mean that despite best efforts, everything in an enclosure needs to be ready to stand up to the heat, or total system failure can occur. This extends to non-electric components, like adhesives. In fact, adhesives can aid in the dissipation of heat in critical components, and can help get the engineer out of a sticky situation.
"Thermally conductive adhesives are uniquely qualified to meet the increasingly diverse requirements of advanced electronics systems," says Venkat Nandivada,"From their conventional use as fastening materials, adhesives find wide use in bonding and encapsulation in nearly every application segment, including military/aerospace, medical, automotive, and industrial, among others," Nandivada says. "In computer and communications systems, thermally conductive adhesives have long played a vital role at the chip level for die attach, at the PCB level for heat sink bonding, and at both the chip- and board-levels for all types of thermal management methods."
He continues, "For fast-growing segments ranging from high end electronics to LED lighting and more, engineers need materials to dissipate more heat from advanced electronic devices. In this environment, thermally conductive adhesives not only support a wide range of thermal management requirements but also meet equally challenging requirements for manufacturing assembly and extended product life cycles. Additionally, many of these thermally conductive adhesives are designed to provide resistance to 85 C, [and] 85 percent relative humidity reliability testing."
Wafer thin
Master Bond's Nandivada notes that adhesives also have to have size, weight, and power consumption (SWaP) in mind when making epoxies, silicones, light curing systems, polysulfides, polyurethanes, and cynoacrylates for the aerospace and military industries.
"Although thermally conductive adhesives have long played an important role in electronics manufacturing, industry trends are driving a more critical need for these materials," Nandivada says. "As the semiconductor industry pushes toward smaller, higher density devices, product manufacturers face greater challenges in assembling die, package, and other components into products able to cope with increasing heat loads."
He continues, "One key requirement tends to be the need for thin bond lines to be applied to maximize heat transfer and minimize thermal resistance. Along with heat transfer in many cases there is a critical requirement for electrically non-conductive adhesives with low dielectric constant and low dissipation factors at high frequencies. In certain situations, there may even be a need for electrically conductive adhesives which provide low volume resistivity. These adhesives need to not only meet growing thermal requirements, but also meet unique manufacturing and life cycle requirements dictated by the needs of the application. WithThe good news for SWaP-minded engineers is that a thin bond line of is actually preferable to thick as it helps reduce thermal resistance and increase heat dissipation.
"The particle size of the thermally conductive filler in the adhesive can contribute to a trade-off between optimal bond strength and optimal heat transfer," says Master Bond's Nandivada. “The bulk thermal conductivity specification addresses only part of the objective of internal heat transfer. In a typical product assembly, a more practical characteristic is the material’s thermal resistance. Thermal resistance describes the ease with which heat can transfer across the interface between the die or component surface and bonding material, across the bonding material, and finally across the interface between the bonding material and package or heat sink.
Speed and heat
Advances in semiconductor process technologies boost not only speed, but also heat in today's military and aerospace systems. That problem may grow -- literally -- as the U.S. Department of Defense (DOD) eyes development future electronics architectures that involve 3D heterogeneous integration (3DHI) chip stacks.
Earlier in the year, Military + Aerospace Electronics reported on the U.S. Defense Advanced Research Projects Agency (DARPA) releasing an announcement (HR001123S0019) for the Miniature Integrated Thermal Management Systems for 3D Heterogeneous Integration (Minitherms3D) project as the government looks for a way to keep the 3DHI chip stacks cool.
In a 3D stack, hot spot thermal management must rely on in-tier heat spreading, since interior tiers do not have direct access to top or bottom cooling. In a Si tierThe project highlights a growing need by the military and aerospace industry to use every bit of available space in increasingly tight confines to solve heat issues.
"The ability of thermally conductive adhesives to help dissipate heat has motivated their use as the preferred fastening approach in applications requiring careful thermal management," says Master Bond's Nandivada.
Playing defense
Although adhesives play a crucial role in mission success outside of embedded computer systems, researchers in China are using epoxy not just to protect separate internal components, but in an entire weapons system. Study lead Gao Lihong noted in the peer-reviewed Chinese-language journal Ordnance Material Science and Engineering publication on 17 May 2023 that using a cheap solution to protect reported success in using a resin that has shown efficacy as an anti-high-energy laser protective coating on ballistic missiles.
The Alibaba Group-owned South China Morning Post reported on the discovery in a story titled "Could this 1-dollar Chinese adhesive defeat a billion-dollar US laser weapon?"
SCMP journalist Stephen Chen reported that the researchers applied a 2.5-millimeter coating made primarily of boron phenolic resin (BPR), which is used in high heat and high stress environments. "This solution uses low-cost raw materials, a simple manufacturing process and has very high performance," says Gao and her colleagues in the paper.
In fact, the adhesive costs approvable $1 per kilogram (2.2 pounds). Chen's reporting notes that a high-energy laser could burn a whole through the thin BPR coating in seconds, but the team added readily available inorganic compounds like silicon carbide, zirconium dioxide and carbon black nanopowder to protect the aerospace aluminum alloys.
"BPR-1 and other recent advancements in protective technology are pushing the directed energy weapons arms race between the United States and China to a new stage, according to a Beijing-based laser scientist," Chen writes in the SCMP piece.
"Welcome to Star Wars 2.0," said the researcher, who Chen said requested not to be named due to the sensitivity of the technology.
Sticky situations
Practical applications for military and aerospace-grade adhesives is as varied as the industry itself. Snipers are known to seal threads on their clothing with silicone to protect it while in the field and on mission, while aerospace engineers need adhesives that stand up to the rigors of supersonic flight and the conditions of space.
Master Bond's EP3TS-TC fast curing, silver filled, one-part epoxy meets National Aeronautics and Space Administration (NASA) requirements for low outgassing in outer space, high vacuum conditions in optical and electro-optical applications, among others. Master Bond's EP3HTS-TC cures rapidly at 250 to 300 F with minimal flow and low shrinkage upon curing.
Its main use is as an adhesive for die attach and general bonding purposes. EP3HTS-TC bonds well to a wide variety of substrates including metals, composites, ceramics, and many plastics. It is well suited for automatic dispensing equipment and can be applied without any tailing.
For other types of bonding, it combines remarkable thermal and electrical conductivity. In fact, the thermal conductivity exceeds 16 W/(m·k). Along with this, the maximum particle size is about 20 microns, and when these numbers are combined, the thermal resistance is a 1-5 x 10-6 K·m2/W.
Other desirable attributes include resistance to thermal cycling, and a low coefficient of thermal expansion. The temperature range is -80°F to +400°F. Two scenarios in which EP3HTS-TC would be a top candidate include in applications where the lowest possible volume resistivity is required. Another is when pre-eminent thermal conductivity is necessary and the need for electrical conductivity is not a pertinent issue.
Master Bond also offers its EP5TC-80 epoxy for use in bonding, sealing and small encapsulation applications. EP5TC-80 is a special system. Master Bond says that a typical, unfilled epoxy is highly electrically and thermally insulative with a thermal conductivity value of about 0.25 W/(m•K). Adding filler materials that conduct heat and not electricity, generally increases thermal conductivity. EP5TC-80 is able to achieve up to 3.3-3.7 W/(m•K).
According to Master Bond, this system bonds well to a wide variety of substrates such as metals, composites, ceramics and many plastics. The filler material has ultra fine particles, with the largest being 10 go 15 microns, which designers can use in very thin sections. The end result is very low thermal resistance. The combination of fine bond lines and thermal conductivity lowers the thermal resistance to 6-10 x 10-6 K•m2/W.
EP5TC-80 resists water, oils and fuels. It is gray in color. The service temperature range is -50 to 150 C. With its robust thermal conductivity, it can solve thermal management issues in aerospace, electronics, opto-electronic, and specialty OEM applications. EP5TC-80 is a versatile system which can be used for bonding heat sinks to circuit boards, coils and motors, die attaching in optics, bonding SMDs, potting power modules and encapsulation of very small coils.
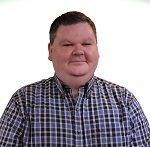
Jamie Whitney
Jamie Whitney joined the staff of Military & Aerospace Electronics and Intelligent Aerospace. He brings seven years of print newspaper experience to the aerospace and defense electronics industry.
Whitney oversees editorial content for the Intelligent Aerospace Website, as well as produce news and features for Military & Aerospace Electronics, attend industry events, produce Webcasts, oversee print production of Military & Aerospace Electronics, and expand the Intelligent Aerospace and Military & Aerospace Electronics franchises with new and innovative content.