Navy approaches industry for new materials and manufacturing for microwave vacuum tubes used in radar
CRANE, Ind. – U.S. Navy radar experts are approaching industry to find alternative electronic manufacturing and materials for microwave vacuum tubes because existing materials are expensive and difficult to obtain.
Officials of the Naval Surface Warfare Center Crane Division (NSWC-Crane) in Crane, Ind., issued a request for information (N0016421SNB27) on Wednesday for the Thoriated Tungsten Replacement for High Power Microwave Vacuum Tubes project.
Navy experts are trying to find companies able to develop alternative domestic manufacturing processes for thoriated tungsten wire or develop wires with alternative chemistries and equivalent operational characteristics to replace thoriated tungsten wire.
Processes that companies can develop under this process will help the Navy build and sustain high-power microwave devices that use thoriated tungsten wire until 2045, and potentially longer, officials say.
NSWC-Crane is responsible for sustaining deployed Navy radar. Experts note that several deployed radar systems rely on microwave vacuum tubes containing an emissive thoriated tungsten filament cathode to amplify the radar signal.
As vacuum tubes operate over time, the emissivity of the thoriated tungsten filaments decays due to the evaporation of the thorium. Technicians can restore the quality of thoriated tungsten by taking the tubes apart and replacing the filament.
Radar designers use thoriated tungsten in tube filaments because of its outstanding electron emission capabilities. The thorium oxide within the wire provides an effective source of electrons, and the tungsten enables the wire to operate at high temperatures without deforming.
Today, however, the traditional supply of high reliability, high temperature, thoriated tungsten wire is dwindling, hence the need to find new ways to manufacture it, or find environmentally friendly new materials that can substitute for it in microwave vacuum tube designs.
Related: DOD's abhorrence of microwave tubes
Navy experts are looking for new ways to produce thoriated tungsten with a minimal amount of hazardous waste, or find a new non-hazardous manufacturing process to produce a near-equivalent to today's thoriated tungsten chemistries.
Current versions of the wire are about one percent thorium oxide, and the rest is high-quality tungsten. Thorium oxide is finely distributed throughout the wire to provide consistent electron emission, yet surface coatings with the same lifetime and performance are acceptable. The wire must have a low work function and resist deformation under temperatures hotter than 1,600 degrees Celsius.
Finding new chemistries may involve alloys cerium and lanthanum with tungsten wire, and other chemistries with equivalent performance and lifetime also are of interest.
Related: L-3 builds microwave tubes for AMRAAM missiles
Proposed solutions must have about the same performance as thoriated tungsten wire; measure 0.006 to 0.010 in diameter; be able to handle six to eight volts AC and 93 to 106 amps; and operate in temperatures as high as 1,500 to 1,700 C.
Companies interested should email six-page responses no later than 26 Feb. 2021 with pertinent company information, which of the two kinds of solutions they will pursue, and specifics of their solutions to the Indiana Innovation Institute at [email protected].
More information is online at https://beta.sam.gov/opp/a54892a040e14f558f0aec00b324e6fa/view.
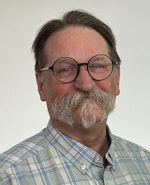
John Keller | Editor-in-Chief
John Keller is the Editor-in-Chief, Military & Aerospace Electronics Magazine--provides extensive coverage and analysis of enabling electronics and optoelectronic technologies in military, space and commercial aviation applications. John has been a member of the Military & Aerospace Electronics staff since 1989 and chief editor since 1995.