Test and measurement equipment keeps high-tech systems in working order
NASHUA, N.H. - Military vehicles — crewed and uncrewed — are packed with an incredible amount of technology necessary to complete dangerous and complicated missions. Soldiers, sailors, Marines, airmen, and space warfighters must have confidence that these machines of war will operate as intended, and their armaments will work when needed. To meet that goal, the U.S. Department of Defense (DOD) and its private-sector partners rely on accurate test and measurement equipment.
Oscilloscopes, spectrum analyzers, and software-defined test equipment contributes to mission readiness.
“These instruments provide important confirmation of system or bus performance before being placed in real-world environments like flight or defense systems,” says Chris Loberg, director of mainstream oscilloscope applications at Tektronix Inc in Beaverton, Ore. “For example, an oscilloscope can confirm the operation of a critical control bus under a variety of simulated conditions.”
Angus Robinson, a product manager at Anritsu America in Morgan Hill, Calif., notes that accuracy and traceability in measurements is key to provide confidence.
“For example, all communications networks rely on key metrics such as frequencies, timing, and signal levels. Without the ability to set these parametersIn control
National Instruments Corp. (NI) in Austin, Texas, produces automated test equipment. Its global go-to-market leader of aerospace and defense, Nick Butler, notes that with software-defined test and measurement equipment, the user is in control of the equipment’s functionality.
“Contrast this to vendor-defined or fixed-function test equipment where you’re essentially limited to the functionality and routines prescribed by the vendor,” Butler says. “With software-defined test equipment, functionality can be customized and modified over time to meet changing requirements or even to repurpose the equipment across different projects or programs. This is especially important and valuable for mil-aero customers for several reasons. One is the rapid pace of innovation. Requirements are constantly changing to adapt to adversarial threats.
He continues, “Take electronic warfare (EW) systems, for example – EW systems must be able to handle and respond to new signals and data signatures provided by ELINT teams. And the pace at which new counter measures must be developed leaves no room for changing test hardware. But when you can adapt through software to prototype and deploy new algorithms quickly, using the same commercially available hardware, you can keep pace with threats and maximize mission readiness. And with trends towards cognitive and autonomous radar and EW systems, the role of onboard software – and the ability to rapidly design and test that software – is increasingly important. Another great example is long life cycle programs, which are very common in mil-aero applications – with software-defined test and measurement equipment, companies can ensure that equipment can last the duration of a program’s lifetime, adapting over time to comply with new security standards, accommodate technology insertions, evolve test program sets, and keep mission-critical assets operational at all times.”
On the line
Retired U.S. Air Force Maj. Gen. Stephen Sargeant, who is the CEO of Marvin Test Solutions in Irvine, Calif. says that his company shines in assuring arms are tested and mission ready.
“The armament consists of bomb racks, launchers, pylons, all their sub components that make weapons work when they’re supposed to and not operate when they’re not supposed to be operating,” Sargeant says. “So, our test equipment ensures that warfighters have the highest level of readiness with the minimal amount of time and effort expended.
Sargeant explains that with reliable test and measurement equipment and comprehensive testing, non-working line replaceable units (LRUs) can be tracked down and quickly replaced and the affected armaments can be sent to the depot for overhaul or modernization and ensure it will last for the duration of its planned life cycle, often an additional 10 or 15 years from the time it is sent to skilled technicians.
Marvin Test Solutions, Sargeant says, is helping the Air Force achieve their desired goals. According to Sargeant, Gen. Charles Q. Brown, Jr., the Air Force Chief of Staff, operates under the mantra “accelerate change or lose.”
“So [Gen. Brown has] got his entire force leaning forward in the innovative space to ensure that they can pick up and deploy rapidly in ways they haven’t necessarily done, in some cases, forever,” Sargeant says. “In some cases, all the way back to World War II before, and it’s called agile combat employment has been the concept of maintenance that has been settled upon as the concept of maintenance, that they’re going to focus their energy on it. So, we have paying attention to that. As it’s been emerging, we looked at our test equipment that we had and said we were kind of thinking about that ahead of time in some ways, because we make our test equipment not only easy to use, easy to maintain, sustainable, we make it very rugged and deployable with a very small footprint. What I mean by that is a lot of the equipment that goes to the flight scientists to maintain tests and sustain armament takes multiple people to carry multiple boxes, large boxes, two main carry types out to the flight line, and then we’ll take hours and hours to run tests.”
Trends in test
Peter Blume, the founder and president of Bloomy Controls, Inc., a provider of automated test solutions, noted a quartet of trends in test and measurement in the mil-aero sector. They are digital transformation; autonomy; electrification, and technology migrations.
“Large portions of the industrial sector are only just beginning to recognize the value that digital transformation can offer development, manufacturing and test,” Blume says. Of these, test seems to be the last to adopt the principles of digital transformation. Bloomy is actively driving these principles into the test equipment sector by providing Thread-Ready test systems to customers who are only beginning to integrate model-based systems engineering (MBSE) tools and techniques into their products’ digital threads.”
Regarding autonomy, Blume says that “Bloomy has noticed an increasing trend away from putting humans in harm’s way or into situations which would otherwiseBlume notes that because air and ground vehicles are fully embracing electric and hybrid power, including air taxis, vertical take-off and landing (VTOL), that electrification is driving development in test and measurement equipment.
Finally, Blume addressed technology migrations impacting trends in test and measurement in the mil-aero sector.
“Many older military and commercial aircraft programs are supported by antiquated test equipment comprised of instruments and computers that are increasingly difficult to support and replace. Add to that the ‘gray wave’ of retiring engineers who designed and maintained the equipment for years, and we find ourselves in a risky situation where we are either holding our collective breath, hoping that the equipment doesn’t fail, or we are making gradual upgrades, while hoping that the necessary downtime doesn’t interfere with any unforeseen test requirements,” Blume says. “In response to these issues, Bloomy has teamed up with partners such as NI and Alta Data Technologies to host the HIL Technology Evolution Center, an industry-first initiative to help aerospace and defense organizations reduce the risk and cost of migrating legacy test assets to updated technologies.”
Anritsu’s Robinson also says that with technology becoming ever more sophisticated and radio frequency (RF) communications using more complex modulations, “the requirements on test equipment could easily become overwhelming. Military and aerospace customers are increasingly in need for test solutions that self-configure to eliminate user error in the field.
Margaret Grattan, market solutions and business manager at Tektronix, notes that test and measurement technology — like nearly all military tech — is being impacted by open systems mandates.
“In the U.S., our customers are adopting a Modular Open Systems Approach (MOSA) in the development of new defense systems. This is happening as a result of the still relatively recent major defense acquisition programs (MDAP) mandate,” Grattan says. “Given many of these defense systems must manage and process a great deal of data at high throughputs, our customers are partnering with us to help them on their plans for the testing of high-speed interfaces, including modules and backplanes. Our expertise in physical layer test and measurement, and our decades-long involvement in setting standards for high speed interfaces in particular, has resulted in a great alignment of Tektronix solutions and customer problems.”
In the field
Marvin Test Solutions was recognized by Military & Aerospace Electronics as a platinum-level awardee in its 2020 Innovators Awards for the company’s MTS-3060A SmartCan Gen2 universal O-level aircraft armament test set.
Marvin Test’s Sargeant says that with the SmartCan, “Those units that have it as they migrate from one aircraft to another in the future, they can actually take the SmartCan with them, and it can be used across all of their fixed or rotary wing armed aircraft, whether they’re manned or unmanned. So, it provides a great level of flexibility for them.”
Current testers require many personnel to move to the flightline and to operate, and are too slow and cumbersome to validate faults, reducing combat sorties. Warfighters have identified an armament test gap that exists across legacy and 5th generation aircraft equipped with the “Smart” weapon MIL-STD-1760 interface. Legacy handheld O-Level test sets are only capable of performing stray voltage and continuity tests which will not detect digital faults or fully validate the functionality of the interface, requiring the use of additional, multiple large box test sets to more completely test the armament.
The MTS-3060A SmartCan Universal O-Level Armament Test Set was developed to address these needs; the result is an advanced flightline armament test setNI’s Butler noted the company’s USRP X410 software defined radio device shows how the company is responding to trends in mil-aero test and measurement.
The Ettus USRP X410 features a two-stage superheterodyne architecture with four independent transmitter and receiver channels. It also features a Xilinx Zynq Ultrascale+ RFSoC with programmable FPGA supporting the Open Source UHD tool flow as well as LabVIEW FPGA. With these features, the Ettus USRP X410 has the RF and processing performance for applications such as wireless communications prototyping, spectrum monitoring, and signals intelligence.
“With the pace of innovation in communication, radar, and electronic warfare systems, being able to rapidly prototype new protocols and algorithms is critical toTektronix recently released its MSO6B series oscilloscope, which the company says provides mil-aero customers with a more precise, lower-noise measurement instrument.
“The MSO6B enables engineers to see levels of detail in a test system that could not be visualized with prior generations of digital oscilloscopes,” says Textronix’s Loberg. “In addition to measurement accuracy; the MSO6B contains up to 8 each measurement channels; delivering on a trend to view a greater variety of measurements on a common display/timescale.”
Bloomy’s Blume says that his company has a complete offering of battery management system (BMS) test equipment for the BMS product development life cycle.
“The BMS is an embedded system that monitors and balances the cells, optimizes the performance and ensures the safety of the battery. During BMS validation and HIL testing, the battery cells are simulated using either real cells or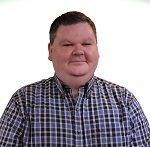
Jamie Whitney
Jamie Whitney joined the staff of Military & Aerospace Electronics and Intelligent Aerospace. He brings seven years of print newspaper experience to the aerospace and defense electronics industry.
Whitney oversees editorial content for the Intelligent Aerospace Website, as well as produce news and features for Military & Aerospace Electronics, attend industry events, produce Webcasts, oversee print production of Military & Aerospace Electronics, and expand the Intelligent Aerospace and Military & Aerospace Electronics franchises with new and innovative content.