The shrinking world of small-form-factor embedded computing
NASHUA, N.H. - Whether on the ground, at sea, or in the air, military systems like monitors, sensors, and radios are filled with small-form-factor embedded computing technologies. Open-systems standards like C4ISR/EW Modular Open Suite of Standards (CMOSS), Sensor Open Systems Architecture (SOSA), and Future Airborne Capability Environment (FACE) help to ensure components share a common platform and can interchange information across military branches.
Peter Thompson, vice president of product management at Abaco Systems in Huntsville, Ala., says he has observed a trio of trends advancing development in the world of small-form-factor embedded systems. First, Thompson says, is alignment with CMOSS and SOSA.
“The CMOSS initiative was begun by the U.S. Army’s Communications-Electronics Research, Development and Engineering Center (CERDEC) and SOSA was initiated by the U.S. Air Force’s Life Cycle Management Center,” Thompson says.
Regarding the Zynq Ultrascale+ RFSoC, Thompson says it is one of the densest field-programmable gate array (FPGA) digital signal processor (DSP) boards available on the market.
“(It) features the ability to synchronize multiple boards for even larger system applications,” Thompson says. “Boards such as Abaco’s 3U VPX VP430 that implement this technology are designed for some of the ‘hottest’ applications across the electronic warfare landscape — MIMO (multiple input/output), beamforming, sensor processing, and radar signal processing.”
The Abaco VP430 was among the first 3U VPX commercial off-the-shelf (COTS) solution to feature Xilinx ZU27DR RFSoC technology. It also has eight A/D converter and D/A converter synchronized channels, and it can synchronize several boards for large system applications.
Designed for advanced electronic warfare (EW) MIMO applications, the VP430 enables beamforming, sensor processing, and radar signal processing, and allows the use of fewer boards and much less power while delivering increased processing throughput.
Eyes on SOSA and CMOSS
Thompson also says that Abaco’s SBC3511 rugged 3U VPX single-board computer was developed specifically in response to the requirement for alignment with the SOSA and CMOSS standard.
“Recently, at the Georgia Tech Research Institute (GTRI) Tri-Service Open Architecture event in Atlanta, we were able to highlight our experimentation successes with the Army and the EW Planning and Management Tool,” says Thompson. “Prolonged efforts with the Army to demonstrate Abaco CMOSS alignment and SBC3511 capabilities culminated in a successful “plug and play” demonstration in a government-designed chassis.”
He continues, “What’s interesting is that demand for CMOSS- and SOSA-aligned solutions isn’t only coming from the U.S. armed forces. As the U.S. represents the majority of the market for military embedded computing, armed forces in other territories can clearly see what the future holds and are asking for similar solutions.”
The SBC3511 offers memory resources including 32 gigabytes of high speed DDR4 SDRAM and as much as 256 gigabytes NAND Flash (NVMe solid-state drive), plus a range of I/O including DisplayPort, USB, GPIO and serial comms. An on-board mezzanine expansion site is also provided for enhanced system flexibility.
The SBC3511’s Data Plane fabric connectivity is via a 40G-capable Ethernet fat pipe, with a Gen 3 capable PCI Express fatAvailable in a range of air- and conduction cooled build levels with extended temperature capability, the SBC3511 is designed to meet the requirements of a wide range of applications from industrial through to fully rugged defense and aerospace programs.
Trends in embedded tech
At January’s Embedded Tech Trends (ETT) conference in Atlanta, Curtiss-Wright Defense Solutions of Ashburn, Va., was one of many companies on hand to “talk shop” about rugged small form factor computing. Curtiss-Wright’s Ivan Straznicky, who is the chief technology officer (CTO) for the Virginia-based company’s Advanced Packaging division, explained that 5G, Internet of Things (IoT) and artificial intelligence (AI) are three big trends driving development.
“What’s next is going to be dependent on how creative we can get,” Straznicky told his ETT industry contemporaries and conference attendees. “But that doesn’t necessarily mean recreating the wheel from scratch. There is a lot of work that has been done with commercial small form factor standards in VITA and other standards bodies. So, we should leverage what we can.”
The Curtiss-Wright CTO says that in addition to 5G, AI, and IoT, system-in-package technology is starting to provide additional functional density.
Straznicky explains system-in-package as “potentially a piece of silicon from a processor vendor like AMD or maybe even Intel and combine it with memory chips from Micron and you put that on the same substrate and create a package.”
Straznicky says that the Defense Advanced Research Projects Agency’s (DARPA) Common Heterogeneous Integration and Intellectual Properties Reuse Strategies (CHIPS) program aims to use system-in-package technology. “They have some long-range strategies and plans to leverage this for defense applications,” Straznicky says.
Smaller than small
Curtiss-Wright Senior Product Manager Mike Southworth says that “DuraNet 20-11 one of the smallest mini gigabit Ethernet switches; it weighs half-a-pound. U.S. and foreign [militaries] are using it in so many capacities it brings with size and weight reduction. The cards are purpose-built to be extremely small.”
The DuraNet 20-11 is made for harsh environments such as high altitude, extreme shock and vibration, extended temperatures, humidity, dust and water exposure, and noisy electromagnetic interference. The switch can help enhance C4ISR capabilities for unmanned air and ground vehicles and other SWaP-constrained platforms deploying network connectivity at the tactical network edge.
Mini and modular
Curtiss-Wright’s Southworth selected the company’s DuraCOR 312 as another example of how it is tackling small-form-factor computing.
The mission computer features six Armv8 processor cores and 256 Pascal/CUDA-core GPU along with multiple add-on I/O and storage expansion options to support additional vetronics/avionics interfaces. The unit comes with on-board eMMC Flash and supports an optional internal M.2 solid-state drive (NVMe/SATA), as well as optional removable 2.5” SATA solid-state drive storage for high capacity storage and information assurance requirements.
Small footprint
Pentek in Upper Saddle River, N.J. made news at ETT when its experts announced the company’s Quartz model 5550, a SOSA-aligned eight-channel A/D and D/A converter, 3U OpenVPX board based on the Xilinx Zynq UltraScale+ RFSoC.
“The model 5550 is leading the industry in the rollout of products developed in alignment with the Technical Standard for the SOSA Reference Architecture,” said Bob Sgandurra, director of product management of Pentek. “Pentek continues to be very active in the development of the SOSA technical standard and we are now demonstrating our commitment with supporting products and demonstrations.”
The front end accepts analog RF inputs on eight coax connectors located within a VITA 67.3D backplane connector. After balun coupling to the RFSoC, the analog signals are routed to eight 4 GSPS, 12-bit A/D converters. Each converter has built-in digital downconverters with programmable 1x, 2x, 4x and 8x decimation and independent tuning. The A/D digital outputs are delivered into the RFSoC programmable logic and processor system for signal processing, data capture or for routing to other resources. A stage of IP based decimation provides another 16x stage of data reduction, ideal for applications that need to stream data from all eight A/D’s. Eight 4 GSPS, 14-bit D/A converters deliver balun-coupled analog outputs to a second VITA 67.3D coaxial backplane connector. Four additional 67.3D coaxial backplane connections are provided for clocks and timing signals.
Scaling down
Mercury Systems in Andover, Mass., says that technology itself is driving the industry’s ability keep things shrinking in the world of small-form-factor embedded systems.
Mercury’s Senior Product Manager Shaun McQuaid says, “One of the bigger trends we’re seeing is as things get smaller, they’re getting closer to the sensor. As they get closer to the sensor, they get smaller, and so what that means for us is that we’re actually starting to invest much more significantly in the kind of chips and chiplet areas creating specialized silicon that is really oriented towards that kind of size, weight and power constraints.”
McQuaid says what was once at the board or box level has shrunk onto a single chip. “I think what is driving development is really the need to bring that compute power up directly into the platform and closer and closer to the sensor,” McQuaid says.
“Think about artificial intelligence and machine learning. The idea that you can leverage the most modern AI technology and put that in service of image recognition or infrared recognition or signal recognition ... that means that the amount of data that these platforms are gathering can be sifted much more effectively and much more quickly when that processing is done right up against the sensor,” he says.
These developments can help solve computing bottlenecks, McQuaid continues. “So rather than having this large amount of data either stored and collated for later or beamed to the ground in dribs and drabs for someone else to look at or even dropped on the floor, if you don’t have the processing horsepower to deal with it, with those kind of technologies right up against the sensor on the platform at the tactical edge, you have the ability to get actionable information to the warfighter much more quickly, much more efficiently.”
Eyes on AI
Mercury has introduced the EnsembleSeries HDS6605 powerful general-purpose 6U OpenVPX embedded computing blade server with hardware-enabled support for AI applications.
The HDS6605 is SWaP-optimized and has increased scalability via ultrapath interconnect. Each 6U OpenVPX blade provides as many as 22 cores from one 1.9 GHz processor, delivering 2.6 teraFLOPS of general-purpose processing power. EnsembleSeries HDS6605 server blades offer advanced packaging, cooling, and interconnects to protect the blades from harsh environments.
Earlier this year, Mercury unveiled its EnsembleSeries SFM6126 OpenVPX PCI Express (PCI Express) gen 3 switch, which is also made with space-constrained embedded computing in mind and is suitable for AI, EW, and autonomous platforms.
The rugged 6U modules can switch the control and expansion planes to support the inter-module data distribution architecture required by high-performance OpenVPX high-performance embedded edge computing (HPEEC) subsystems.
“One of the latest trends in commercial data centers is to use a composable infrastructure,” says Joe Plunkett, Mercury’s vice president and general manager for sensor processing solutions. “This allows the computing, storage, and switch fabric resources to be individually aggregated, disaggregated, and composed based on an application’s precise needs, giving system architects much greater flexibility in deploying and reconfiguring resources as needed.”
Mercury officials say their company’s SFM612 delivers more processing power by pre-integrating other EnsembleSeries HPEEC building blocks including server-class processing blades, FPGA and NVIDIA GPU co-processing engines with a wideband, low-latency and universal PCI Express HPEEC architecture.
Small-form-factor in space
Microchip Technology in Chandler, Ariz., has launched what company officials claim is the industry’s first space-qualified Ethernet transceiver.
Microchip’s VSC8541RT radiation-tolerant Ethernet transceiver is a radiation-tolerant device based on a COTS solution widely deployed in other industries now offering reliable performance for applications ranging from launch vehicles to satellite constellations and space stations.
The VSC854RT has a total ionizing dose of 100 krad(Si), and a no single event latch-up below an LET threshold of 78 MeV.cm2 /mg at 125 degrees Celsius.
The device supports a wide range of LVCMOS levels for a parallel MAC interface including: 1.5, 1.8, 2.5, and 3.3 volts, as well as 1.2, 1.5, 1.8, 2.5 volts, and 3.3-volt support on the MDIO/MDC interface.
This space-qualified version of the product adds ceramic and hermetic packages, extended temperature range of -40 to 125 C, and extended qualification flow equivalent to QML-V or QML-Q space grade.
Microchip officials also announced that their company has received final qualification for the new SAM3X8ERT rad-tolerant microcontroller, which features its latest Arm Cortex-M3 core processor and embedded Ethernet controller.
The VSC854RT and SAM3X8ERT are COTS-based and share the same pin-out distribution, allowing designers to begin implementation with COTS devices before moving to space-grade components.
“Microchip’s COTS-based space-grade processing provides the right performance and the right level of qualification to meet evolving requirements from Low-Earth Orbit constellations to deep space missions,” says Bob Vampola, associate vice president of Microchip’s aerospace and defense group.
The SAM3X8ERT features ARM Cortex-M3 revision 2.0 running at clock speeds as high as 84 MHz, no single event latch-up below an LET Threshold of 62 MeV.cm2 /mg at 105 C, and a total ionizing dose of 30 krad(Si).
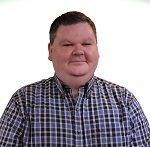
Jamie Whitney
Jamie Whitney joined the staff of Military & Aerospace Electronics and Intelligent Aerospace. He brings seven years of print newspaper experience to the aerospace and defense electronics industry.
Whitney oversees editorial content for the Intelligent Aerospace Website, as well as produce news and features for Military & Aerospace Electronics, attend industry events, produce Webcasts, oversee print production of Military & Aerospace Electronics, and expand the Intelligent Aerospace and Military & Aerospace Electronics franchises with new and innovative content.