Electronics cooling boosts capabilities to match performance upgrades
NASHUA, N.H. - Here’s the good news: electronic and electro-optic subsystems for aerospace and defense applications progressively are becoming higher performance, smaller sized, and lighter weight. Now here’s the bad news: all those benefits have a major system tradeoff: a growing amount of waste heat.Â
It’s a fact of life that aerospace and defense systems designers can’t escape: the higher the performance and the smaller the size, the greater the amount of heat that designers must confront. It’s not as though electronic components can be designed economically that can tolerate huge amounts of heat. Instead, designers have to find ways to cool these ever-hotter electronic components, and they must do it affordably, and in small, lightweight packages.
“We are seeing higher heat densities year after year,” points out Bryan Muzyka, manager of sales and marketing at Advanced Cooling Technologies Inc. in Lancaster, Pa. “The intelligence and defense contractors are trying to build electronic systems in smaller packages, so the waste heat is going up.”
How to deal with waste heat in electronics can be as much of an art as it is a science. Designers have many options with which to attack the problem, ranging from industry-standard approaches to custom designs, depending on the customer’s needs and budget. Almost always, however, the designer must strike a delicate balance among capability, ruggedness, component size and weight, and costs.
Essentially the challenge of electronics cooling and thermal management boils down to three choices: conduction cooling, air cooling, and liquid cooling. Each of these options varies in cost, complexity, and in the amount of heat they can eliminate.
Conduction cooling
Perhaps the most widespread and best-known thermal management approach for rugged aerospace and defense applications is conduction cooling. TheseConduction cooling often calls for wedge-lock devices along the edges of circuit cards to help transfer heat from the card, along rails, through the chassis, and eventually to the outside of the chassis where it is dissipated.
“Conduction cooling is by far the biggest cooling approach in terms of COTS hardware out there,” says Ivan Straznicky, chief technology officer of advanced packaging at the Curtiss-Wright Corp. Defense Solutions segment in Ashburn, Va. “Still, as power goes up, it becomes more difficult for conduction-cooled modules to handle cooling.”
Despite increasing power consumption in embedded cooling, designers won’t be writing-off conduction cooling any time soon. For many applications, its capacity to control system temperatures is perfectly adequate, and systems designers are finding new ways to stretch the limits of conduction cooling in increasingly hot systems.
Curtiss-Wright’s Straznicky, for example, says his company is using conduction cooling for embedded computing modules today that dissipate as much as 200 Watts of waste heat, whereas only a few years ago conduction cooling reliably could remove perhaps half that amount of heat.
Other designers have similar experiences. “Four years ago we looked at 80 Watts for a 3U conduction-cooled card, and now we are up to 100 Watts,” says Brian Hoden, principal mechanical engineer at Abaco Systems in Huntsville, Ala. “We are pushing the limitations in traditional conduction cooling.”
Among the reasons for the enduring popularity of conduction cooling are relatively low costs and its inherent rugged design. Conduction cooling has no moving parts, as opposed to air and liquid cooling. No moving parts means fewer parts at risk of failure, and the card-edge wedge locks that go along with conduction cooling can protect sensitive electronics from the ill effects of shock and vibration.
One well-known and often-followed open-systems industry standard for embedded computing conduction cooling is the VITA 48.2 standard, set forward by theVITA 48.2 applies to 3U and 6U VPX embedded computing modules, and defines the dimensions of plug-in units for conduction-cooled applications and connector-mounting details, as well as key sub-rack interfaces, to facilitate two-level maintenance and interoperability among different vendors.
A big part of pushing the limitations of conduction cooling lies in the innovation that VITA 48.2 allows, says Curtiss-Wright’s Straznicky. “It is in the interfaces, but on top of the module, where you can do some things to improve your cooling, such as different cooling materials to improve the thermal interface between the electronics and the frame.”
Much of this type of technology innovation, however, remains proprietary to the companies doing the design work, and so cannot be described in detail.
Much of the innovation in conduction cooling, however, involves the card wedge lock, says Abaco’s Hoden. “The wedge lock is an area where we have put a lot of work into for conduction-cooled cards; we have our own wedge lock design,” he says. “The card-to-chassis interface is really neglected in our industry, but represents one of the biggest temperature rises in an electronic chassis.”
Air cooling
Another common and effective thermal management technique involves using moving air to transfer heat away from sensitive components. This can be as simple as using an internal fan to blow air over hot components, much like people see in laptop or desktop PCs.
While air cooling is relatively inexpensive, however, this approach presents several challenges to the aerospace and defense systems designer — chief among them being reliability. Cooling fans are mission-critical moving parts that can fail at the worst possible time, as many designers have found. Plus, moving air can introduce contaminants like dust and corrosive vapor into the system, which can cause their own problems.
VITA 48.8 is for advanced air-flow-through cooling in high-performance embedded computing and RF and microwave such as military avionics. It describes an approved approach to designing with air-cooled plug-in modules using 3U and 6U VPX circuit cards while retaining the VPX connector layout. It helps reduce weight and cost for high-density, high-power electronic systems by eliminating wedge locks and ejector handles.
The standard permits air inlets at both card edges, as well as on the top circuit card edge opposite the VPX connectors. It also can promote use of polymer or composite materials to reduce chassis size and weight.
Put in practice, the ANSI/VITA 48.8 design approach enabled avionics engineers at the Lockheed Martin Corp. Rotary and Mission Systems segment in Owego, N.Y., to reduce the size and bulk of the avionics computer aboard the Lockheed Martin Sikorsky S-97 experimental high-speed helicopter.
VITA 48.8 improves the efficiency of the thermal path to cool high-performance processors, field-programmable gate arrays (FPGAs), general-purpose graphics processing units (GPGPUs), and other hot components. Unlike tradition air cooling, the standard specifies gasketing to prevent particulate contamination from the moving air.
“This is a big deal because you don’t need wedge locks with VITA 48.8; you use jackscrews,” says Abaco’s Hoden. “It is still rugged, but you can remove the card with the jackscrews, and is a way of locking-down the card against vibration. You don’t need an ejector handle like you do with wedge locks.”
The primary design tradeoff of AFT cooling is the need to provide moving air. “Compared to conduction cooling, you need an air source,” Hoden points out. “You get better performance with an air-cooled chassis than you do with conduction cooling, but you need an external fan to cool it.”
A big advantage to VITA 48.8 is its utility with 6U- and 3U-sized circuit cards, points out Curtiss-Wright’s Straznicky. “Air flow through enables you to cool more, and is quite effective for 3U, because you have a short span to blow the air. You can get up to 150 Watts of cooling per module on 3U, and up to 250 Watts for 6U.”
Liquid cooling
Just five years ago the notion of liquid cooling for high-performance embedded computing was considered impossible for all but the most demanding and expensive applications. Now liquid cooling is approaching the mainstream.
VITA 48.4 liquid cooling does introduce system complexity and cost, but makes up for it with its ability to cool hot high-performance embedded systems. “At some point you take heat away from the modules with liquid, but then that liquid needs to be cooled down, so somewhere in the system you need a liquid heat exchanger,” Straznicky says.
It’s all about getting cooling liquid to sources of the heat, says Abaco’s Hoden. “Liquid cooling allows you to get the liquid down to the hot spots on a board, and that helps immensely. With liquid you have a lot of options. Liquid flow through will be something we will see a lot more of in the future.”
ACT offers a cooling technology its engineers call Pumped Two Phase (P2P) Cooling, also known as Pumped Evaporative Cooling, which is active cooling that uses the latent energy of boiling liquid to remove high levels of waste heat efficiently.
Compared with single-phase cooling P2P helps lower liquid flow rate, and reduce system size and power consumption. P2P systems allows the working fluid, typically a refrigerant, to boil as it passes through the cold plate and removes the heat from the hot surface of the device. this approach removes more heat than single-phase cooling, which does not allow the cooling liquid to boil, ACT’s Muzyka explains. “The more heat flow, the better your cooling,” Muzyka says. “But the more heat flow, the hotter your fluid becomes.”
ACT also offers a single-phase liquid cooling approach called Pump 2, in which the liquid also boils, but contains the boiling liquid within the flow lines “The advantage of boiling is higher heat loads without failing your electronics. All your components run at a very uniform temperature, and we can have smaller pumps and smaller flow rates to enhance SWaP [size, weight, and power consumption]. We are providing the full system: the cold plates, the pumps, and the heat sinks packaged together.”
The SOSA standard
One of the most influential open-systems embedded computing standards in years is the Sensor Open Systems Architecture (SOSA), which offers component interoperability, rapid innovation, quick technology insertion, reduced costs to the taxpayer, and the ability for defense systems to keep up with the cutting edge of commercial computer technology.
Among the OpenVPX standards that are becoming part of SOSA are the VITA 48.2 specification for VPX microcomputers using conduction cooling; the VITA 48.4 specification for using VPX liquid flow through cooling; and the VITA 48.8 specification for using VPX air flow through cooling.
“SOSA starts with VITA 48.2, which is conduction cooling for both 6U and 3U cards,” says Curtiss-Wright’s Straznicky. “The two others that have been accepted into SOSA are VITA 48.8 air flow through, and VITA 48.4 liquid cooling.”
It’s widely expected in the embedded computing industry that SOSA standards will be requirements in the future for aerospace and defense electronics. If companies already are offering VITA 48.2-, VITA 48.4-, or VITA 48.8-compatible products, then they will have at least part of the SOSA requirements checked-off in future procurements.
“We are looking at VITA 48.4,” says Abaco’s Hoden. There is some interest in this, especially in SOSA, so we have cards that are aligned to the SOSA guidelines.”
Not only have the military services voiced their support for SOSA, but each service sends representatives to SOSA standards-formation committees. This gives the military a voice, side-by-side with industry, in how SOSA standards develop.
Many consider SOSA to be the most dominant and influential of these standards not only because of its military-wide support, but also because its administration comes under The Open Group in San Francisco — an industry consortium in place to promote open, vendor-neutral technology standards and certifications. Until SOSA, the latest standards typically have been military service-specific or platform-specific initiatives.
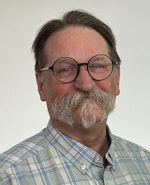
John Keller | Editor-in-Chief
John Keller is the Editor-in-Chief, Military & Aerospace Electronics Magazine--provides extensive coverage and analysis of enabling electronics and optoelectronic technologies in military, space and commercial aviation applications. John has been a member of the Military & Aerospace Electronics staff since 1989 and chief editor since 1995.