It may be next year before defense electronics supply chain recovers completely from the COVID-19 pandemic
FORT WORTH, Texas – While U.S. electronics manufacturing is starting to recover from the COVID-19 pandemic, aerospace and defense systems designers are confronting new market conditions that are making the defense electronics supply chain perhaps as difficult as it was during the depths of the pandemic.
Those involved in the military electronics industry know it's difficult to find components and raw materials for many kinds of electronic systems and subsystems. This time, though, it's not the pandemic that's slowing down the supply chain; it's competition with the commercial electronics industry, which is ramping-up far more quickly than defense manufacturing.
"Most factories have manufacturing back to normal," says Don Akery, president of electronics distributor TTI Americas in Fort Worth, Texas. "What's changed is the suppliers of these components for aerospace and defense have seen only a slight increase in demand, but all the other markets are seeing unusually large increases in demand."
While demand for aerospace and defense electronic components is up 6 percent from the pandemic year of 2020, automotive bookings, for example, are up 60 percent, industrial demand is up 30 percent, communications is up 80 percent, and computing is up 30 percent.
"Demand in all these other segments are increasing at those levels, and in those factories they have been loaded-up with non-aerospace and defense components, so we have to compete for those components," Akery says.
"That's been the lingering impact on the supply chain that started with the pandemic," Akery continues. "Coming out of the pandemic, this increased demand has continued to make the supply chain very tough. Prices have gone up and continue to accelerate."
The weather freeze in Texas last February didn't help, Akery says. "The freeze actually shut down a lot of manufacturing plants, and some of those plants are still not fully operational. Raw materials are not recovering, with connectors most prevalent. Those shortages and prices on resins have gone up dramatically."
One factor that has eased pressure on the electronics supply chain is the pandemic-induced drastic slowdown in commercial aircraft manufacturing. "Commercial aviation has been down as commercial air traffic came virtually to a stop during the pandemic," Akery says. "That actually helped the supply chain because it freed-up capacity."
There's some good news for component lead times -- or the time it takes to receive component shipments after ordering. "I do believe that lead times are not getting additional push-outs; they have stabilized," Akery says. "By the end of this year we will see lead times come down, and it will be next year before they come down to pre-pandemic levels.
Lead times for some components -- particularly for electronic connectors -- continue to be hard-hit. While lead times for interconnect products were eight to ten weeks during the first quarter of 2020, today connector lead times can be as high as 16 to 18 weeks. Those waiting for complex connectors today may have to wait for as long as 36 weeks.
Akery recommends that systems integrators give as much information to their suppliers about their future demands so suppliers can plan for the necessary raw materials, and evaluate capacity in effort to keep supply disruptions to a minimum.
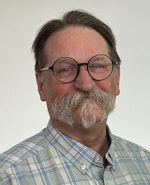
John Keller | Editor-in-Chief
John Keller is the Editor-in-Chief, Military & Aerospace Electronics Magazine--provides extensive coverage and analysis of enabling electronics and optoelectronic technologies in military, space and commercial aviation applications. John has been a member of the Military & Aerospace Electronics staff since 1989 and chief editor since 1995.