NASHUA, N.H. -Â Global demand for affordable satellite communications for applications ranging from cell phone connectivity and television content, to space-based military and agriculture surveillance and monitoring are driving huge increases in small satellites and the radiation-hardened electronics that make them function effectively.
It is this need for radiation hardening that focuses the electronics industry’s efforts on developing components like microprocessors, power-management devices, and solid-state memory that are inexpensive to buy, yet resilient enough to survive in space for periods ranging from weeks to years.
“We are really starting to see four quantums in the satellite space marketplace,” explains Anthony Jordan, director of business development at Cobham Advanced Electronic Solutions Inc. (CAES) in Colorado Springs, Colo. These four quantums consist of small cubesats with mission durations of only 12 to 18 months; business satellites with life spans of two or three years of mission life; so-called “constellation space” with each satellite expected to last in orbit for five to seven years; and finally the long-duration satellites that will operate in geosynchronous orbits for decades.
Four space segments
The first quantum primarily is for proof-of-concept research projects and can accept non-rad-hard components. The second quantum must have limited radiationThe whole idea is to design, test, or upscreen electronic components that are good enough for their intended applications, while keeping size, weight, power consumption, and cost (SWaP-C) to a minimum to meet mission goals.
For the first two quantums little or no radiation hardening is necessary. Radiation shielding and special packaging for tier 2 often is all that’s needed, while for tier one developers most often choose commercialÂ-grade electronic parts from distributors. “We’re talking quick-turn and low-budget,” Jordan says. This tier represents perhaps 20 percent of the space parts market.
Tier 2 sees a lot of specially packaged 6U and 3U electronics subsystems using commercial electronic parts that have been upscreened for enhanced reliability, or automotive parts designed and upscreened for the harsh environmental conditions of passenger cars or commercial trucks.
Satellite failures due to space radiation or other environmental conditions are tolerable for tiers 1 and 2 because the relatively low costs of these spacecraft enable periodic replacement. On-orbit failures become more problematic, however, for tiers 3 and 4.
Tier 3 is among the most interesting space segments because its practitioners aim to deploy and operate economically, but also offer reliable service for each satellite for five to seven years. Tier 4, also called “exquisite space,” is for the most expensive and long-lasting satellites. Often these spacecraft are for military communications and surveillance, and many aspects of their missions are kept secret. The first three tiers often are referred to as “new space.”
Where the money is
When analysts look at the four space segments, “the meat is in the middle,” CAES’s Jordan says. “Quantum two and three are probably the strongest segments for growth, and they represent about 60 percent of the market. Over the next five years I wouldn’t expect to see a lot of growth in Tier 4, and I wouldn’t expect to see a lot of growth in tier 1.”
“I find amazing the number of satellites that are going up,” says Jim Kemerling, chief technology officer of Triad Semiconductor Inc. in Winston-Salem, N.C., which specializes in radiation-hardened electronic components like general-purpose input/output devices, A/D converters, and sensor interfaces.
“Elon Musk said in March that the Starlink system may have 1,200 to 1,300 satellites,” Kemerling says. “But the market has been very fragmented, and still is.” Echoes Malcolm Thomson, president of Radiation Test Solutions (RTS) in Colorado Springs, Colo., “We see continued growth in space applications.” RTS specializes in affordable test and measurement solutions to qualify components for space uses.
Those who will succeed in radiationÂ-hardened space electronics will be those who can ensure reliability, affordability, quick-turnaround designs, and access to the latest semiconductor technologies. Typically that will mean plastic-encapsulated parts, rather than the more expensive hermetically sealed ceramic parts that have been a staple of rad-hard space electronics for decades.
Plastic packaging for space
Apogee Semiconductor in Plano, Texas, specializes in radiation-hardened plastic-encapsulated parts for space applications. “We are space plastics from the ground-up; we don’t have any hermetic ceramic parts in our portfolio,” says Apogee CEO Anton Quiroz. “There are too many performance tradeoffs — in a bad way — with hermetic.”
Perhaps the best aspect of plastic parts is relatively low costs and access to the latest generations of microprocessors, field-programmable gate arrays (FPGAs), solid-state memory, and other electronic components. While ceramic hermetic parts have a reputation for high reliability, they also are expensive, difficult to obtain, and typically lag at least a generation behind their equivalents in plastic-encapsulated parts.
“Plastic is starting to proliferate for space applications,” Quiroz says, adding that factors driving space systems designers to plastic packages are a push for higherRelying on plastic-encapsulated space parts, however, can be a double-edge sword, Quiroz points out. “Companies are buying a lot of plastic parts and doing a lot of upscreening, which can lead to unknown performance.” The costs of upscreening plastic parts, he says, can be like “wrapping a hundred-dollar bill around that five-dollar part. A big risk is they do not have a controlled baseline, and need to do a requalification with the next lot.”
One solution to the problem of high costs of upscreened parts may be in standardized design approaches with known performance. Today Apogee relies on the company’s reputation for high-reliability in plastic space parts, but industry is getting the ball rolling on developing openÂ-systems reliability standards for plastic parts for space.
The JEDEC Solid State Technology Association in Arlington, Va., has formed the JC-13.2 microelectronic devices committee, led by The Aerospace Corporation in El Segundo, Calif., that in as little as two years is expected to lead to a new U.S. government-backed qualification for high-performance plastic space parts, Quiroz says.
The future standard will be MIL-PRF-38535 Qualified Manufacturing List (QML) Class P, and will be administered by the U.S. Defense Logistics Agency (DLA) in Columbus, Ohio. MIL-PRF-38535 is a U.S. military performance specification that establishes the general performance and verification requirements of single-die integrated circuits. It defines quality assurance and reliability requirements for integrated circuits used in military applications and other high-reliability microcircuit applications.
MIL-PRF-38535 space-qualified parts today typically are QML class V, for space-grade parts. These typically are high-performance and high-cost ceramic parts that are difficult to obtain. The future QML class P qualification should make a wide variety of space-grade parts available that are lower cost and higher performance.
For now, however, Apogee manufactures logic function circuits, level translators, and transceivers to the company’s own space-qualification standard, which is based on AS6294/1 for plastic encapsulated microcircuits in space applications, published by SAE International in Warrendale, Pa. Quiroz says these parts will have many similarities to the future QML class P parts. “The reason we are doing plastic is because they will get higher performance than QML class V,” Quiroz says.
There’s a simple reason for the move to QML class P and other plastic packaging for space, says CAES’s Jordan. “The customer wants more capability, and with more capability that means more speed. The organic plastic packages enable us to move things at higher rates.”
Unfortunately ceramic parts run counter to that trend, Jordan says. “In ceramic we see limitations to speed and transfers per second, in a memory device or wired interface. You can’t push 50 gigabits per second through a ceramic package; you really need an organic package like plastic.”
Rad-hard enabling technologies
VORAGO Technologies in Austin, Texas, specializes in radiation-hardened and extreme-temperature solutions for space and high-reliability applications. The company’s patented HARDSIL technology uses high-volume manufacturing to harden commercially designed semiconductor components for aerospace, defense, and industrial applications.
“We implement radiation hardening to existing and commercial parts,” says Garry Nash, chief operating officer at VORAGO. The company’s HARDSIL technology —
short for hardened silicon — is a process enhancement, but not a design for radiation hardening, he says.
This process enables VORAGO experts to fabricate microcontrollers, solid-state memories, and provide design and development tools for rad-hard electronic components that will operate even at higher orbits than low-Earth orbit. “It allows us to provide rad-hard parts up to 300 kilorads, at design times that are close to commercially designed parts,” Nash says. “It costs substantially less.”
VORAGO’s newest product is the VA416XX ARM Cortex microcontroller, which Nash says “has a lot of interest in the space market because it is the most powerful space microcontroller today.” The company also provides radiation-hardened communications for Spacewire, CAN, and Space Ethernet.
VORAGO also offers design analysis tools that can monitor space subsystems to detect and prevent a latchup conditions in non-rad-hard parts. “It allows designers to use non-rad-hard parts in an overall system that will see radiation,” Nash says.
Triad Semiconductor offers what Kemerling says is called a via-configurable array, which is an analog mixed-signal array configured with a via layer. “The key to it working is it is configured with a via layer, but it is mask-programmable, not field-programmable.”
Advanced space packaging
As the size, weight, and power consumption of space electronics components continue to shrink, CAES’s Jordan says systems integrators can expect new kinds of packaging in their electronic components. “We will start to see more use of chiplets and heterogeneous packaging of die,” he says. “We are now bringing microprocessor, serial interconnect, and memory in pieces and putting them together in a system package. Designers also are bringing in A/D converters, D/A converters, and RF components into the package. Now I’m starting to bring the system level together, which involves advanced packaging.”
Jordan says multicore microprocessors for space have evolved from two, to four, and now to eight cores for low-Earth orbit applications. CAES offers the quad-core GR740 processor, and is developing the eight-core GR765 microprocessor. “The single-, dual-, and quad-core versions all are in production at various levels of life,” Jordan says. “The quad-core processors have flown on spacecraft, and the octal-cores are in development.”
Providing the proper levels of power to these advanced space components will be difficult to develop, Jordan says. “One of the challenges we are seeing is today’s FPGAs are running off of 0.8- and 0.7-volt cores. They are burning 30 to 50 amps at 0.8 volts; that is an interesting challenge.
“CAES has been working to find high-efficiency solutions in this realm,” Jordan continues. “We start with a satellite that we are lucky if it has a 28-volt bus. We have to convert from a 28-volt bus all the way down to 0.8 volts through a couple of conversions. You want efficiencies up around 95 percent, but how do you get that efficiency? That’s a huge engineering challenge.”
Test and upscreening
A common solution for radiation-hardened electronic components is testing and upscreening commercial-grade parts to find those able to withstand the space environment. There are several test and measurement companies that specialize in just that.
Scientic Inc. in Huntsville, Ala., specializes in radiation survivability; radiation-hardened electronics development and test; parts, materials and processes; and high“We offer not only radiation-effects modeling, but also understand the requirements,” says Barry Posey, director of component engineering at Scientic. “You need to understand quality and reliability levels, and the radiation capability of parts that you plan to add to your system. We also bring radiation-effects testing, which is necessary to guarantee a product in a nuclear environment. That’s what we offer.”
Scientic experts have experience not only in characterizing electronic components, but also in the several kinds of radiation environments that today’s satellites will face in different orbits.
“In the geosynchronous space area you worry most about cosmic rays and some proton levels. But in new space that is variable. For new space low- and mediÂum-Earth orbits you need to be concerned with the orbital inclination and altitude you will fly at,” Posey says. “In addition you may have a lot of the radioactive particles being trapped that you have to worry about. The models we use try to give us an idea what the environment will be at any orbit and altitude we might be flying at.”
3D Plus, a HEICO company in San Leandro, Calif., also specializes in radiation-hardened electronics test and measurement for space, but the job is getting progressively difficult. “What is changing is we are using more and more complex technologies,” says Timothee Dargnies, chief executive officer at 3D Plus.
“Frequencies are faster, and for space electronics the challenges are that those devices are more and more complex to evaluate. You see that across the industry. People need more devices that perform even better. Evaluation of radiation is getting more and more complicated.”
Radiation Test Solutions specializes in radiation-hardened test and evaluation methods that are substantially less expensive than traditional radiation testing, which must be done at places like University of California at Berkeley, Texas A&M University in College Station, Texas, and at Brookhaven National Laboratory in Upton, N.Y.
At places such as this, “there is more work than there is available time,” RTS’s Thomson says. Instead, RTS experts test for single-event upset resistance with lasers, rather than with actual radiation. “There are a lot of advantages of using lasers,” Thomson says. “You don’t have to have a special facility, and with a laser system you can do that evaluation very quickly early on.”
The disadvantage, however, is laser and actual radiation testing do not compare exactly. Still, laser screening can work for components intended for low-Earth orbit, because lasers give a good-enough result for the LEO environment. “Lasers are a screening tool, but they also are a part qualification tool for the LEO folks who need an approximate result,” Thomson says. RTS now is installing laser test equipment at the company’s facility in Colorado Springs, Colo.
“I do believe this test method will be used heavily in the future, and will be sufficient for many satellite applications, particularly for new space, as well as for traditional space for silicon designers, to quicken the design process early on,” Thomson says.Â
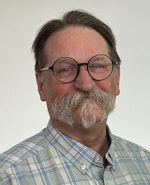
John Keller | Editor-in-Chief
John Keller is the Editor-in-Chief, Military & Aerospace Electronics Magazine--provides extensive coverage and analysis of enabling electronics and optoelectronic technologies in military, space and commercial aviation applications. John has been a member of the Military & Aerospace Electronics staff since 1989 and chief editor since 1995.