NASHUA, N.H. - Radiation-hardened processors, memory, power supplies, and other components for space applications have gone through big changes over the past several years, beginning with a transformation from expensive radiation-hardened-by-design parts to full commercial off-the-shelf (COTS) parts to accommodate a new generation of small satellites and cubesats for new-space uses.
Today, however, the pendulum is starting to swing slowly back in a conservative direction, with more designed-in radiation hardening and test procedures than have been evident in the recent past. The Wild West of anything-goes small satellites with full-COTS parts appears to be coming to a close, as systems designers, component manufacturers, and radiation-hardened test houses report their customers are moving back in the direction of space-reliable parts — at least more than they have in the past several years.
They’re not going back nearly as far as the old days of monolithic spacecraft with super-rad-hard parts and a money-is-no-object design approach. Instead, today the space industry is seeing a move to enhance reliability for the space environment, but still are requiring plastic-packaged parts, with some enhanced testing.
This is a noticeable departure from the early days of the NewSpace era, when full-COTS parts were the norm, and the prevailing attitude centered on quick spacecraft replacements in case of on-orbit failures. Now the approach is somewhere in the middle, with the need to keep costs down, accommodate some of the latest high-performance computing components, and enhance reliability such that on-orbit glitches are somewhat rare, and operators can compensate for problems as they crop up.
NewSpace refers to the emergence of the private spaceflight industry, spanning areas such as private launch companies, small satellite constellations, or sub-orbital tourism, as well as other efforts that aim to reinvent the traditional space industry supply chain.
Ruggedizing COTS parts
Recent experiences of placing pure-COTS parts in space has led NewSpace designers to put more thought into some levels of ruggedization for space components. This is not to say the COTS approach has been abandoned — far from it — but industry consensus is coming around to some levels of value-add for space parts.
“One of the biggest trends I’m seeing is with some of the small satellites they are becoming more stringent, and trying to demand more from the satellite,” says Anton Quiroz, CEO of radiation-hardened parts supplier Apogee Semiconductor in Plano, Texas. “We are starting to see customers leverage radiation-hardened parts more — but they still want them in plastic packages.”
Systems designers have found that using pure-COTS parts can be risky, depending on the application, and has led to unanticipated on-orbit failures that can destroy or degrade the performance of NewSpace satellites. “When you think of COTS, you don’t know what you’re going to get,” Quiroz says. “Even if it’s the same part number, it could have completely different radiation performance; it can vary greatly from lot-to-lot.”
The solution often involves starting with pure-COTS parts and designing a test and measurement regimen to help prevent unexpected on-orbit systems failures or performance degradation. “You don’t want to throw up a bunch of space junk,” Quiroz says. “We want to stay below radiation rates of components, so upscreening can be imperative — and that is expensive.”
Instead, Apogee Semiconductor is turning to automotive-qualified electronic components from different chip fabs, which often can provide adequate ruggedization to survive the space environment. “We want to use the low-cost commercial nature of these parts,” Quiroz says. “We package all our parts in plastic, rather than in ceramic, and we use automotive-type test and screening.”
The trick is testing just enough to meet the application and the radiation environment. “We see the amount of commercial space, where most customers are not looking for a full [reliability] screening, and we are giving them a touch of radiation screening,” says Marti McCurdy, CEO of radiation-tolerant integrated circuit designer Spirit Electronics in Phoenix. “We do a bit of dynamic burn-in, and then some burn-in. We are not seeing full-MIL-883 testing as much as we used to.”
Negotiating the middle ground between extensive radiation testing and non-tested full-COTS use can provide “faster time to market and is less expensive than running the full gamut of testing,” McCurdy says. Selective radiation testing also encourages space systems designers to pay close attention to specific space applications that may or may not require addition radiation testing, he says.
Balancing risk and costs
Systems designers must balance the risks, costs, and potential payoffs of which parts they choose ultimately for their spacecraft. “If a constellation needs 40 small satellites, and you have to get them into orbit, single-event upset might mean the loss of one spacecraft. They will risk that one loss, because they have 39 other satellites up there. They need to make a choice of moving forward or not launching at all,” McCurdy says.
In addition, Spirit Electronics experts find different means of enhancing the reliability of electronic parts intended for space. “We will collect all published data and make an assumption of whether the part will meet or exceed the customer specification,” McCurdy says. “The market also is asking for commercial products that are radiation-tested. We are meeting commercial space applications with COTS products with radiation data, so these parts can be flown in space.”
Word is out that space systems designers are taking a second look at space-qualified components. “We are seeing more and more requests for our radiation-assured parts; we are seeing that from a lot of customers,” says Mike Tsecouras, product line manager for optocouplers, sensors, and displays at space electronics supplier Micropac Industries Inc. in Garland, Texas.
Micropac specializes in radiation-tolerant optocouplers, which are semiconductors that enable transmission of electrical signals between two isolated circuits. Optocouplers have two parts: an LED that emits infrared light, and a photosensitive device that detects light from the LED.
“The trend is, from the optocoupler side, that industry has been looking to see how well it will work in the space environment. Micropac is going after that directly, and we offer DLA [U.S. Defense Logistics Agency]-certified optocouplers.” Tsecouras says his company is trying to fill a need in the radiation-hardened electronics industry.
“It was often the case in the past that companies may provide parts, and the onus is on the customer to do their own testing and qualification, based on their program needs. We want to shorten that, and make it easy for the customer to get access to, buy, and use parts managed by the Defense Logistics Agency. Micropac is investing in die banking and pre-testing to ensure these products are readily available.”
In addition to demonstrated radiation performance, Tsecouras says Micropac’s customers are looking for part traceability to help document systems designs so satellite manufacturers and the government can learn from what works in space, and what doesn’t.
“They are trying to do their designs quickly, and part of parts selection is even based on what’s available on the market. They can’t take a build-to-order custom part; they don’t have the schedule for that. They need radiation traceability to each device number.”
The different orbits in which NewSpace satellites must operate, ranging from relatively benign low-Earth orbit (LEO) to geosynchronous and polar orbits, which have much higher exposure to space radiation. “In our parts selection, we know the degradation that these different orbit environments will cause, and we pre-select device that will incur the degradation and still be spec-compliant,” Tsecouras says.
Traditional space
It’s clear that NewSpace is driving today’s radiation-hardened electronics applications in largely private ventures that involve widespread Internet access, Earth observation, on-demand entertainment, and space-based research. NewSpace is time- and cost-driven, and differs significantly from government-funded space initiatives in which costs and the speed of deployment often are not top concerns.
Nevertheless, traditional space initiatives still are viable concerns — especially for crewed and uncrewed deep-space exploration missions, government-sponsored large-area weather observation and forecasting, and military-sponsored reconnaissance and surveillance satellite projects.
“We also support traditional space, and our process enables us to do that,” says Apogee’s Quiroz. “We have product releases in different radiation levels, ranging from LEO to deep space. Traditional space isn’t going away. There is a continued need for geostationary satellites with a high level of radiation tolerance.”
The extreme radiation environments of geosynchronous orbits, polar orbits, and deep-space missions are not the places for enhanced COTS electronic components; these represent a need for components that are designed from the ground-up to be radiation hardened. These applications typically are long-duration, impossible to repair once lofted into space, and are subject to some of the harshest-known radiation environments.
“For LEO, most of the satellites have some protection from the Earth’s magnetic field, so the devices have some protection,” says Steve Singer, product marketing manager of Renesas Electronics, a rad-hard chip designer in Palm Bay, Fla.
“Harsher environments are in geosynchronous orbits,” Singer continues. “Our customers are still building satellites for geosynchronous orbits, so that market is not going away.”
High-performance space computing
Another force behind today’s space electronics is the emerging need for high-performance computing in orbit to handle growing demand for digital signal processing, image processing, advanced networking, and the artificial intelligence (AI) and machine learning that will define the next generation of space missions.
To get there, the spacecraft industry needs radiation-hardened high-performance general-purpose processors, field-programmable gate arrays (FPGAs), general-purpose graphics processing units (GPGPUs), A/D and D/A converters, optocouplers, and many other kinds of components.
“High-performance computing in space is a big focus for our customers,” says Renesas’s Singer. “They are looking for their satellites to be smarter, with a higher level of intelligence and machine learning. Then we see commercial space applications that are about potential data centers in space, which involves new architectures and processors — traditional rad-hard processors, and some new FPGAs that are high-performance and rad-tolerant. There also is a large customer base looking for rad-tolerant ASICs [application-specific integrated circuits].”
Such capabilities are not limited only to NewSpace applications. “Even on the government side we are seeing a need for AI and machine learning to enable satellites that can respond with little human interaction,” Singer says. “The need is for processors that have multiple cores and operate at high clock speeds. The architectures for cell phones are making their way into space applications, and people are trying to make them rad-hard.”
The need for AI and machine learning in satellites isn’t just for image and signal processing, experts point out. AI and machine learning also will be central to the kinds of machine autonomy technologies that will enable large and exquisite satellites of previous generations with constellations of small satellites that must operate reliably as teams.
“How do you manage a large satellite? I takes a lot of people on the ground,” points out Michel Sika, CEO of Lucid Circuit Inc. in Santa Monica, Calif. “We will need to replace each large satellite with several smaller ones, with a limited number of ground stations, and that will be very challenging. We must have management capabilities aboard each satellite, with edge AI capabilities to have satellites take care of basic parts of satellite management.”
The key enabling technology for achieving this will be trusted AI. “How can you enable the satellite to manage operations, test it, and make sure that it is reliable? Now we have the problem of trusted AI,” Sika says. “As AI makes a decision, a human on the ground validates the decision the AI agent makes. Over time the AI agent will be more effective, and can put more management on the satellite.”
In this kind of distributed satellite architecture, satellites must communicate among themselves and aggregate their sensor capability. “That is the next challenge,” Sika says — and all the circuitry necessary to do so much be radiation tolerant.Â
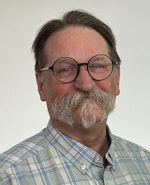
John Keller | Editor-in-Chief
John Keller is the Editor-in-Chief, Military & Aerospace Electronics Magazine--provides extensive coverage and analysis of enabling electronics and optoelectronic technologies in military, space and commercial aviation applications. John has been a member of the Military & Aerospace Electronics staff since 1989 and chief editor since 1995.